
charge in dry grinding ball grinding mills
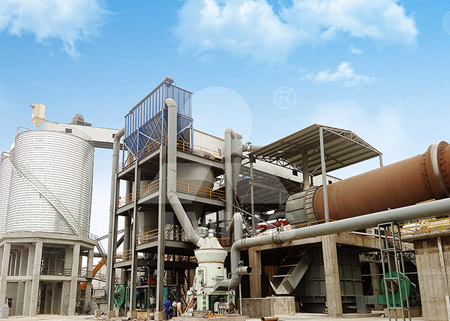
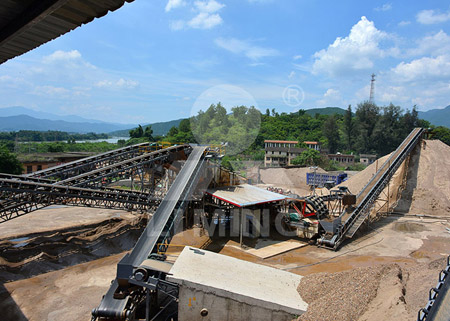
charge in dry grinding ball grinding mills
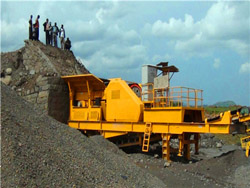
Measurement system of the mill charge in grinding ball mill circuits
Investigation of a dry fine grinding circuit has shown significant influence of the mill load (powder filling) on the production capacity. To improve the circuit performance at industrial scale, alternative ways of mill load measurement were An analysis of the kinetics of dolomite grinding in a dry ball mill reveals that the following approximations apply for the parameters of the batch grinding model: (PDF) Analysis of ball mill grinding operation using mill power
احصل على السعر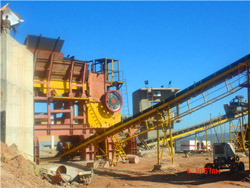
Experimental study of charge dynamics in a laboratory
Abstract. To understand and describe the behavior of charge dynamics in mills, a series of dry and wet grinding tests were performed on a laboratory-scale ball The described mill load measurement was applied to a dry grinding mill circuit. However, the measuring system can also be applied to wet grinding mills, where Measurement system of the mill charge in grinding ball
احصل على السعر
(PDF) Grinding Media in Ball Mills-A Review
One of the most used tumbling mills is the ball mill. This paper reviews different types of grinding media that have been developed and improved over the years and their properties.For dry tests, the orthogonal analysis indicates that the influence order of four factors on power-mass ratio is ball filling, mill speed, powder-grinding media ratio Experimental study of charge dynamics in a laboratory-scale ball
احصل على السعر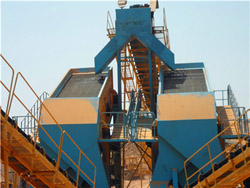
Experimental study of charge dynamics in a laboratory-scale ball
To understand and describe the behavior of charge dynamics in mills, a series of dry and wet grinding tests were performed on a laboratory-scale ball mill. The the grinding media and the ball size distribution of the charge, is also discussed. 2.2 Breakage mechan ism in tumbling ball mills Several mechanisms contribute to the grinding action that takes(PDF) Effect of ball size distribution on milling
احصل على السعر
A specific energy-based size reduction model for batch grinding ball mill
The ball mill is so common that it is utilized for primary, secondary, and tertiary grinding and regrinding in industries including mineral, cement, and coal; in dry or wet grinding processes; andExperimental Investigation on a Grinding Rate Constant of Solid Materials by a Ball Mill Effect of Ball Diameter and Feed Size. Powder Technology, Vol. 143/144,2004, 196-203. 10.1016/j.powtec.2004.04.014 Search in Google ScholarGrinding in Ball Mills: Modeling and Process Control Sciendo
احصل على السعر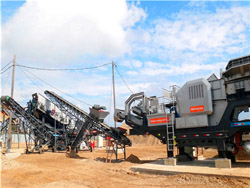
Grinding Mills Ball Mill Rod Mill Design Parts PDF Scribd
HP=HP per ft of mill length. W=Weight of grinding charge and material per ft of mill length. C=Distance in feet from center of mill to the center of gravity of the grinding media. a=Dynamic angle of repose of grinding charges, usually 43° for dry grinding slow speed ball mill, 51° for normal ball mill speeds.A 7 ft diameter dry grinding diaphragm mill has a 40 percent ball charge and a speed of 23.6 rpm. What is the horsepower per foot of length? The mill has 2 in. thick shell liners. From graph, Fig. 3, 12, mill having 6 ft 8 in. inside diameter will have 4400 lb of balls per ft of mill length. Assume material in voids weighs 10% of ball charge.Grinding Mills 911 Metallurgist
احصل على السعر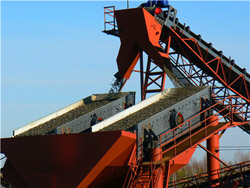
Measurement system of the mill charge in grinding ball mill
Generally, mill rotational speed, charge load as well as lifter height variations reflected well in the mill noise emission. This study supports the use of mill acoustic sensing technique to understand different grinding conditions in AG/SAG mills for improved and continuous process monitoring, energy-efficient milling, and enhanced By means of motion analysis of the charge, a good grinding efficiency can be obtained when the ball filling ranging from 20% to 40% and the mill speed ranging from 70% to 80%. For dry tests, the orthogonal analysis indicates that the influence order of four factors on power-mass ratio is ball filling, mill speed, powder-grinding media ratio Experimental study of charge dynamics in a laboratory-scale ball mill
احصل على السعر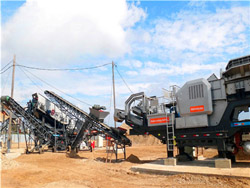
(PDF) Assessment of the Performance of Grinding Circuit for
Ball mill feed and product particle size distribution for survey 1, 2 and 3 Figure 8 to Figure 11 and Table 11 to Table 13 present the results for the size distributions and some key performanceThe starting point for ball mill media and solids charging generally starts as follows: 50% media charge. Assuming 26% void space between spherical balls (non-spherical, irregularly shaped and mixed-size media will increase or decrease the free space) 50% x 26% = 13% free space. Add to this another 10%-15% above the ball charge for total of 23%Ball Mill Loading Dry Milling Paul O. Abbe
احصل على السعر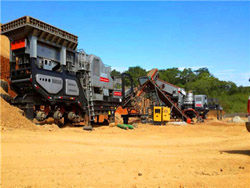
Ball Mill an overview ScienceDirect Topics
Tumbling ball mills or ball mills are most widely used in both wet and dry systems, in batch and continuous operations, and on a small and large scale. Grinding elements in ball mills travel at different velocities. Therefore, collision force, direction and kinetic energy between two or more elements vary greatly within the ball charge.We carried out a detailed study on the effect of particle load and ball load on grinding kinetics. by carrying out experiments at two different mill speeds (55 and 70 % critical) and four levels(PDF) Analysis of ball mill grinding operation using mill power
احصل على السعر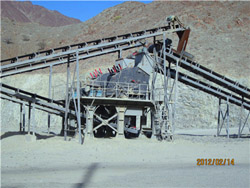
Experimental study of charge dynamics in a laboratory-scale ball mill
By means of motion analysis of the charge, a good grinding efficiency can be obtained when the ball filling ranging from 20% to 40% and the mill speed ranging from 70% to 80%. For dry tests, the orthogonal analysis indicates that the influence order of four factors on power-mass ratio is ball filling, mill speed, powder-grinding media ratio It gives examples of the aspects of grinding and illustrates some general guidelines to follow for modelling processes in planetary ball mills in terms of refinement, synthesis' yield and(PDF) Process Engineering with Planetary Ball Mills
احصل على السعر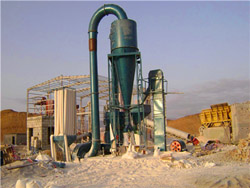
Morgardshammar Grinding Mills PDF Mill (Grinding) Nature
Morgardshammar Grinding Mills Free download as PDF File (.pdf), Text File (.txt) or read online for free. The object of the grinding process is a mechanical reduction in size of crushable material (ores, industrial minerals, rocks, cement clinker, porcelain). Grinding can be undertaken in many ways. The most common way for high capacity industrial Hogg and Fuerstenau [] using an approximate model of the motion of the ball charge derived a simple equation relating mill power to mill dimensions, speed of rotation, and the ball filling level.In this model, it was assumed that the charge consists of two distinct regions: a “static” region where particles do not move relative to the mill shell The Evolution of Grinding Mill Power Models SpringerLink
احصل على السعر
Exploring ball size distribution in coal grinding mills
Request PDF On May 1, 2014, M.M. Bwalya and others published Exploring ball size distribution in coal grinding mills Find, read and cite all the research you need on ResearchGateFor raw mills it is most common to use a ball charge with the coarse grading (up to 50% of 90 mm balls) see table below for “coarse” grading. 36 4.4.4 Cement Mill. The ball charge tendency in the 1st compartment is to use the coarser of the gradings available. When producing high Blaine Cement it is the objective to use less tonnage.1 Ball Mills 1 PDF Mill (Grinding) Gases Scribd
احصل على السعر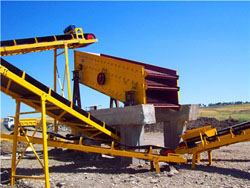
Identifying the apparent and true grinding limit University of
the stirred media mill after a specific energy input of 82,000 kJ/kg. Further studies into the grinding limit in comminution processes were described by Koch [10], Karagedov and Lyakhov [11], Boldyrev et al. [12] and Cho et al. [13]. Koch and Karagedov investigated the minimum achievable grain size in dry grinding processes in planetary ballGrinding Mills. Grinding is the last stage in the comminution process where particles are reduced in size by a combination of impact and abrasion, either dry, or more commonly, in suspension in water. It is performed in cylindrical steel vessels that contain a charge of loose crushing bodies—the grinding medium—which is free to move insideChapter 7. Grinding Mills Wills' Mineral Processing Technology,
احصل على السعر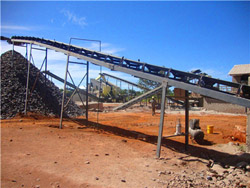
Dry grinding in planetary ball mills: Evaluation of a stressing
Section snippets Experimental set-up. The dry grinding of alumina was performed in a planetary ball mill PM400 (Retsch GmbH) with a sun wheel radius R SUN of 150 mm and a gear ratio of k = −2. The gear ratio is defined as relative rotational speed of grinding chamber n GC in relation to the rotational speed of the sun disc n SUN: k = n
احصل على السعر