
process of clinker grinding
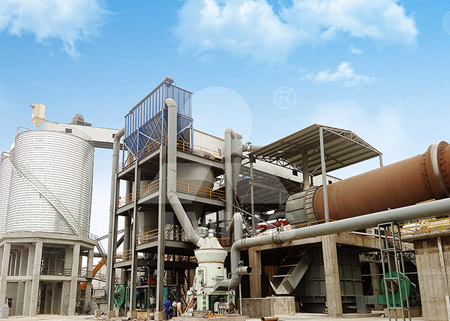
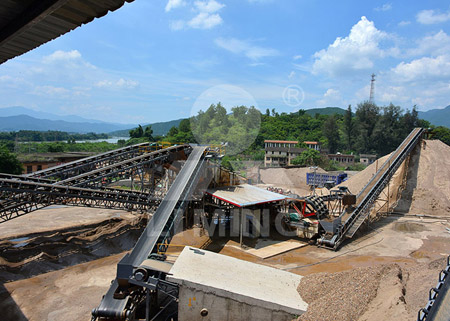
process of clinker grinding
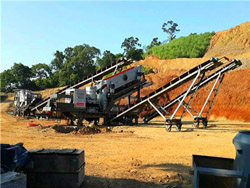
PAPER OPEN ACCESS The grinding clinker pressure
The article describes the grinding process by pressure in order to study the effect of pressing on the fineness of grinding at its different granulometry. Experimental In cement and other mineral processing plants, grinding process requires a considerab le amount of power. Grinding of the clinker consumes about 1/3 of the power required to produce 1 ton...Design of clinker grinding system; mill and
احصل على السعر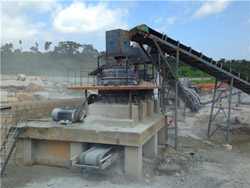
(PDF) Clinker grinding process and cement
Grinding Aids reduce particle re-agglomeration during and after the milling process so improving the yield. Strength enhancers push The cement manufacturing process consists, basically, of the calcination and in the fusion of a material constituted by, approximately, 94% (w/w) of limestone, 4% Experimental study of clinker grinding in a ball mill and
احصل على السعر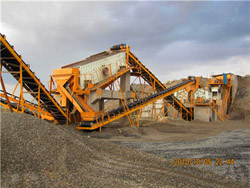
Efficiency of grinding stabilizers in cement clinker processing
Clinker grinding represents the most energetically demanding part of the production process and grinding stabilizers (very often known as “grinding activators”, CONVENTIONAL CLINKER GRINDING -A NEW APPROACH TO THE PREDICTION OF POWER CONSUMPTION Conference: Presented at the Ultrafine (PDF) CONVENTIONAL CLINKER GRINDING -A NEW
احصل على السعر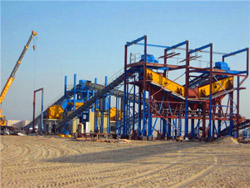
Experimental study of clinker grinding in a ball mill and the
In this paper, the method was used to study the collisions between grinding media and grinding media and walls in ball mills, which is the most used unit operation in Recently, some of us reported that crude glycerol obtained as a by-product of biodiesel manufacture (bio-glycerol) is an excellent concrete additive that is capable of enhancing cement performance by (i) improving the Investigation of glycerol polymerization in the
احصل على السعر
Influence of Clinker Microstructure on Grinding Efficiency in
The mechanism of action of surfactants on the course of the clinker grinding process has not been fully studied. According to the theory of P.A. Rebinder, Grinding (A) 1. Introduction. The goal of the present paper is to discuss the evolution of the chemistry and engineering of the production process of Portland cement as it can be detected from the literature published in this area since the 12th International Congress on Chemistry of Cement [1], [2]. The chemistry of Portland cement clinker hasChemistry and engineering of the production process: State
احصل على السعر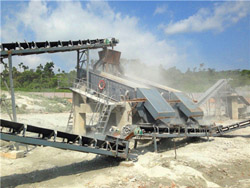
Grindability of mixtures of cement clinker and trass
It is common knowledge that energy consumption in cement clinker grinding circuits is a significant portion of the total electrical energy used. The effectiveness with which the energy invested in the grinding process is utilized depends on, besides many other material- and machine-dependent factors, the particulate environment in which theGrinding of clinker consumes power in the range of 2.5 kWh/ton of clinker produced. These and other pyroprocessing parameters make cement production costly. The pyroprocessing process in kilns and A Review on Pyroprocessing Techniques for
احصل على السعر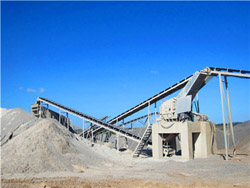
Clinkerization an overview ScienceDirect Topics
The grinding process differs depending on the pyro-processing process used. The feed to the kiln is called “raw meal.” Clinker is produced by pyro-processing the raw meal. The raw meal is burned at high temperatures, first by calcination of the materials and then by clinkerization to produce clinker. Various kiln types have been usedThe inclusion of high specific surface materials such as calcined clays in cementitious systems enhances the hydration of clinker products at very early ages, but it may also increase water demand; thus, the pursuit of a flowing concrete may demand an increase in the dosage of superplasticizers. The grinding regime can have a major Minerals Free Full-Text The Challenge of Grinding Ternary
احصل على السعر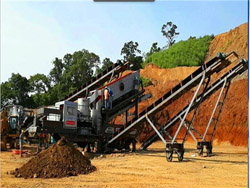
AVAILABLE AND EMERGING TECHNOLOGIES FOR
to improve efficiency since the cooling air has been preheated during the process of cooling the clinker. After cooling, the clinker can be stored in the clinker dome, silos, bins, or outside in Grinding of clinker, together with additions of approximately 5 percent gypsum to control the setting properties of the cement canClinker grinding technology is the most energy-intensive process in cement manufacturing. Traditionally, it was treated as "low on technology" and "high on energy" as grinding circuits use more than 60 per cent of total energy consumed and account for most of the manufacturing cost. Since the increasing energy cost started burning the benefits Clinker grinding technology in cement manufacturing
احصل على السعر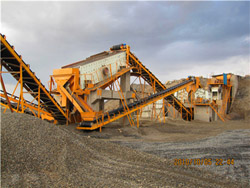
(PDF) Cement and Clinker Production by Indirect Mechanosynthesis Process
The cement and clinker produced by indirect mechanosynthesis (15 min of mechanical activation and heat treatment 900 C or 1200 C) were characterized. In order to test the hydraulic properties ofCement manufacturing includes grinding of the clinker with other additives like gypsum and fly ash. Clinker is manufactured by blending limestone, iron ore and bauxite at high temperatures, with limestone being the key ingredient. Hence, most of the clinker manufacturing plants or cement plants are located in the vicinity of limestone quarries.Emission reduction through process integration and
احصل على السعر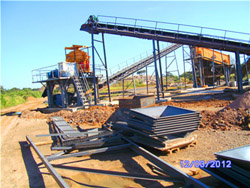
A review of the effectiveness of Life Cycle Assessment for
The dry process includes grinding and heating the raw materials first before feeding them into the kiln, while the raw material is crushed, grounded, and mixed to make a slurry in the wet process. 2.2.3. Production of clinker. The clinker production stage is where the raw material (the raw meal) converts into clinker.Grinding process and clinker factor of the PCC. The clinker was mixed with gypsum and pozzolanic material to produce PCC cement. Plant closed-circuit tube mill used for producing PCC is schematically presented in Fig. 2. Pre-crushed clinker from clinker bin is filled to the hoper feeder before introduced to pre-grinder.Analysis of high clinker ratio of Portland Composite Cement (PCC)
احصل على السعر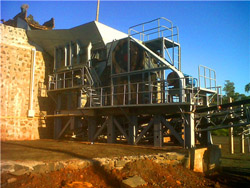
Investigation of glycerol polymerization in the
Cement production is also a highly energy intensive process, and particularly, the grinding of the cement clinker accounts for as much as 40% of the total production cost. Therefore, grinding additives are widely used the process of clinker grinding. Clinker hardness brings about a wide disparity to grindability. About 80% extra power is usually required in processing hard clinker than the soft ones (NwokediEffect of Free Lime and Lime Saturation Factor on
احصل على السعر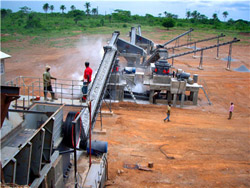
Process technology for efficient and sustainable cement production
The reason for the very limited additional potential savings of thermal energy is the necessary heat for the clinker production process. Fig. 1 shows the heat flows, the thermal input, the use for clinkering and drying, and the remaining waste heat flows that might be utilised. However, the remaining waste heat is already used to a high degree, Coal utilisation in the cement and concrete industries. G. Schumacher, L. Juniper, in The Coal Handbook: Towards Cleaner Production: Coal Utilisation, 2013 15.3.1 Make-up of Portland cement. Portland cement is a fine powder produced by grinding Portland cement clinker (more than 90%), a limited amount of gypsum (calcium sulphate dehydrate Portland Cement Clinker an overview ScienceDirect Topics
احصل على السعر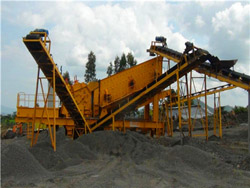
Energy and exergy analyses for a cement ball mill of a
Nowadays, ball mills are used widely in cement plants to grind clinker and gypsum to produce cement. In this work, the energy and exergy analyses of a cement ball mill (CBM) were performed andThe cement grinding plant is a vital link of the finished cement production. The cement grinding plant also called cement grinding unit, is used to grind clinker into qualified cement. With the development of the cement industry, cement grinding plant becomes more common. As an individual section of finished cement production, at this Cement Grinding Plant Overview Cement Grinding Unit
احصل على السعر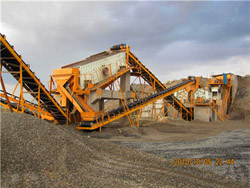
(PDF) Cement grinding optimisation ResearchGate
Clinker grinding constitutes approximately 40 percent of cement production. This grinding process requires a lot of electrical energy (Jankovic et al., 2004). For this reason, various studies areto improve efficiency since the cooling air has been preheated during the process of cooling the clinker. After cooling, the clinker can be stored in the clinker dome, silos, bins, or outside in Grinding of clinker, together with additions of approximately 5 percent gypsum to control the setting properties of the cement canAVAILABLE AND EMERGING TECHNOLOGIES FOR
احصل على السعر
Wear Mechanism of High Chromium White Cast Iron and Its
The detailed deformation mechanism and its microstructural modifications of white cast iron grinding balls used in comminution have been investigated using transmission electron microscopy (TEM) and XRD. De-shaping is the primary mode of ball consumption, and fracture of balls is a relatively uncommon failure mode. Deshaping is
احصل على السعر>> Next:تحليل الفشل في تأثير كسارة المطرقة