
grinding and tool finishing
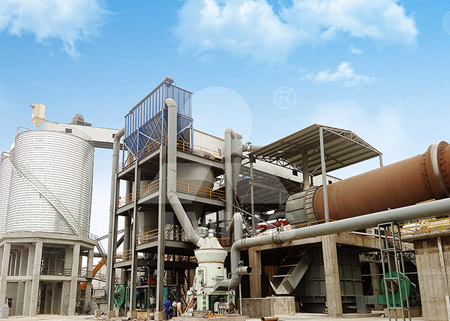
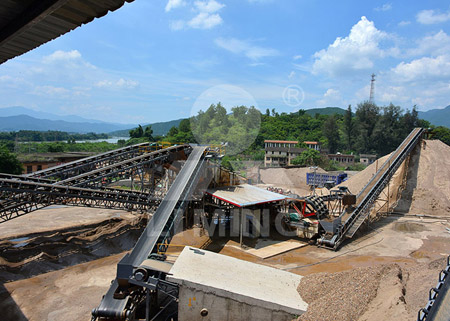
grinding and tool finishing

Cutting, grinding, and finishing The Fabricator
Tip No. 1: Identify Your Desired End Result Knowing what you’re trying to accomplish is the first step in choosing the right abrasive 3M offers a full line of abrasive products and expertise for precision grinding and microfinishing applications. Learn how we can help optimize your precision grinding Precision Grinding and Microfinishing 3M
احصل على السعر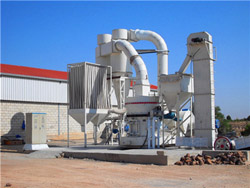
Grinding and finishing processes ScienceDirect
This chapter provides practical data for the selection of grinding and finishing operations applied to these industrial sectors and includes a guide on the Precision grinding requires the hardest minerals and the tightest tolerances. Learn about the technology behind the newest 3M abrasives for precision grinding and finishing, Precision Grinding and Finishing Technology 3M
احصل على السعر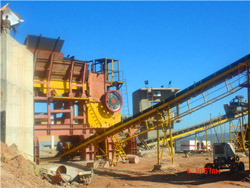
Grinding tool basics: Finish it right The Fabricator
Excessive force is inefficient and can fatigue and stress both the tool and the operator. 6. Use a filter regulator lubricator set at two drops per minute to keep the air clean and lubricated. 7. Before each Centerless grinding. Creep-feed grinding. Cylindrical grinding. Gear grinding. Tool grinding. They all demand precision. And to achieve the highest precision, you need the best abrasives. 3M offers all the Precision Surface Grinding and Microfinishing
احصل على السعر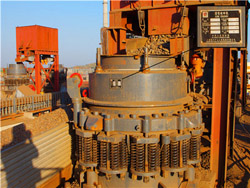
(PDF) Compliant grinding and polishing: A review ResearchGate
Compliant grinding and polishing refers to a class of fine material processing methods relying on one or more system element being compliant with the Attached to the holding mechanism, the grinding or polishing tool is where actual interaction with the workpiece takes place. Developing well-behaved tools Compliant grinding and polishing: A review ScienceDirect
احصل على السعر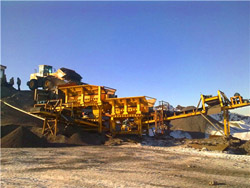
Fine grinding and polishing tools PFERD
The range of fine grinding and polishing tools offers optimum solutions for coarse work on surfaces through to polishing. Whether face-down grinding, belt grinding, peripheral grinding or manual grinding the portfolio includes the best range of coated abrasives and non-woven and felt tool solutions. Register here free of charge for ourFree abrasive tool finishing technology develops rapidly, and it includes a wide range of items, but all feasible finishing methods follow one principle: The abrasive tool (or abrasives) provides certain Surface Quality and Finishing Technology
احصل على السعر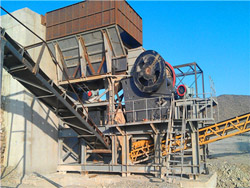
Advanced polishing, grinding and finishing processes for
This article reviews advanced polishing, grinding and finishing processes for challenging manufacturing applications. The topics covered are machining of advanced alloys; machining of wafers; strengths of dies after machining; grinding and polishing for wafer level packages; hybrid finishing processes; magnetorheological finishing; cooling and A 10-amp tool designed to hold media up to 5 in. dia. might grind at 11,000 RPM but perform finishing steps at between 5,000 and 7,000 RPM. That said, the best RPM to use depends on the product being finished and the available amps a power tool has. Speed also changes with the disc diameter.Smart grinding and finishing in the metal fabrication shop
احصل على السعر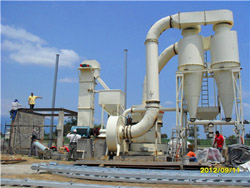
(PDF) Compliant grinding and polishing: A review ResearchGate
Although various polishing techniques such as small-tool polishing [24],magnetorheological finishing (MRF) [25] and ion beam finishing (IBF) [26] have been invented, it still seems difficult toSurface grinding is a finishing process that uses a rotating abrasive wheel to smooth the flat surface of metallic or nonmetallic materials to give them a more refined look by removing the oxide layer and impurities on work piece surfaces. This will also attain a desired surface for a functional purpose. The components of a surface grindingSurface grinding
احصل على السعر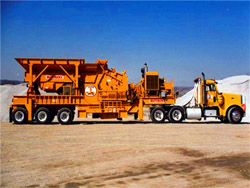
GRINDING PROCESS
Grinding is a surface finishing operation where very thin layer of material is removed in the form of dust particles. Thickness of material removed is in range of 0.25 to 0.50 mm. Tool used is a abrasive wheel Grinding machine is a power operated machine tool where, the work piece is fedPolycrystalline diamond (PCD) tools are widely used in industry due to their outstanding physical properties. However, the ultra-high hardness of PCD significantly limits the machining efficiency of conventional abrasive grinding processes, which are utilized to manufacture PCD tools. In contrast, electrical discharge grinding (EDG) has JMMP Free Full-Text The Performance of Polycrystalline MDPI
احصل على السعر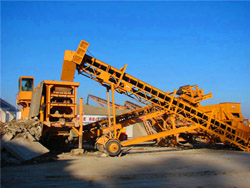
Grinding and finishing. Free Online Library
Free Online Library: Grinding and finishing.(IMTS 2004, International Machine Tool Show) by "Tooling & Production"; Business Metals, TGC 5 is capable of a grinding tool diameter range from 0.0008" to 0.551". Menu-driven software from Numroto and NTI covers drillsMost recently, grinding forces were also modelled for bevel-gear plunge grinding, a typical finishing operation for automotive axle drives [220, 221]. Generating gear grinding is also applicable to beveloid gears i.e., conical involute gears for spatial transmission of power, which is largely used in the latest generation of four-wheel drives [ Grinding and fine finishing of future automotive ScienceDirect
احصل على السعر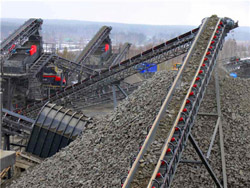
What is Grinding? Hindustan Abrasives
Grinding is an abrasive machining process that uses a grinding wheel or abrasive belt as the cutting tool. It is commonly used to remove material from a workpiece, to produce a smooth finish on the surface of the workpiece, or to remove burrs from the surface. Grinding can be performed wet or dry, and can be performed on a variety of 2002©John Wiley & Sons, Inc. M. P. Groover, “Fundamentals of Modern Manufacturing 2/e” Material removal by action of hard, abrasive particles usually in the form of a bonded wheel • Generally used as finishing operations after part geometry has been established by conventional machining • Grinding is most important abrasive processLesson 6 GRINDING AND OTHER ABRASIVE PROCESSES KSU
احصل على السعر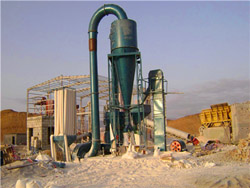
Process design of a novel combination of peel grinding and deep
Klocke developed a machine tool, which combines turning, grinding and deep rolling operations in one machine . In this way, the roughing and finishing of hardened shafts is performed in one setup. This setup includes four cross tables with two grinding spindles, one deep rolling tool and a turret.2. 2 Abrasive Machining • Material removal by the action of hard, abrasive particles usually in a form of a bonded wheel. • Grinding is the most important abrasive machining. Cutting occurs at either the periphery or the face of the grinding wheel. • Cutting occurs by the abrasive grains that are much smaller, numerous and random.GRINDING PPT SlideShare
احصل على السعر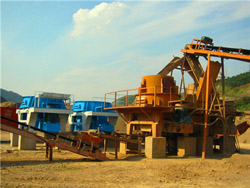
Surface Grinding in Silicon Wafer Manufacturing Kansas State
surface grinding possesses the great potential of producing silicon wafers with lower cost and better quality comparing with its counterparts (lapping for wire- sawn wafers and polishing for etched wafers). In order to fully utilize the potential of surface grinding, however, some technical obstacles will have to be overcome.In this type, the tool is connected to the floating component 1 (Fig. 4(a)). • Type B: Adjustable tool holder. In this case, as shown in Fig. 4(b), component 1 is. Types and schematics. Attached to the holding mechanism, the grinding or polishing tool is where actual interaction with the workpiece takes place.Compliant grinding and polishing: A review ScienceDirect
احصل على السعر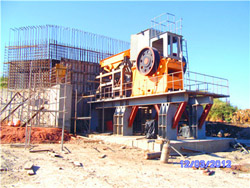
Grinding Machines SpringerLink
Definition. A grinding machine is a machine for material removal with geometrically non-defined, bonded cutting edges, where the relative movement between tool and workpiece is rotational or linear. The machine further must provide relative feed and positioning movements between tool and workpiece. The movements between tool Magnetic abrasive particles are iron-based compound abrasives that have magnetization and grinding ability. Their sizes commonly are 60–200 μm, and they are mainly composed of the magnetic medium phase (usually iron matrix), abrasive phase (abrasive), and adhesive. The structure and grain sizes are shown in Fig. 3.10.Magnetic Abrasive Finishing Technology SpringerLink
احصل على السعر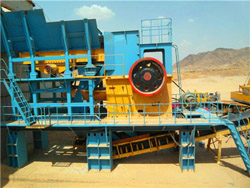
Compliant grinding and polishing: A review ScienceDirect
Fig. 30 shows a variety of fully-compliant tools, including shape adaptive grinding (SAG) tools (the tool body is an air-inflated membrane for tools with diameter more than 20 mm, and silicone or rubber otherwise) [20, 122], rubber based bonnet polishing tools [123], cylindrical tools (silicon rubber) [124], rubber matrix tool [125], flap wheel tool Aluminum and aluminum alloys are among the most used metals in fabrication, construction, and in the creation of good all around you. It is such a useful and versatile metal, but there are some special considerations you need to make when working with it. We have put together this expert guide to fabricating, grinding, and finishing Ultimate Guide Aluminum Fabrication, Grinding, and Finishing
احصل على السعر