
grinding process in iron ore
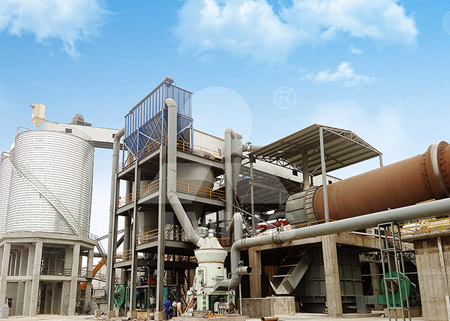
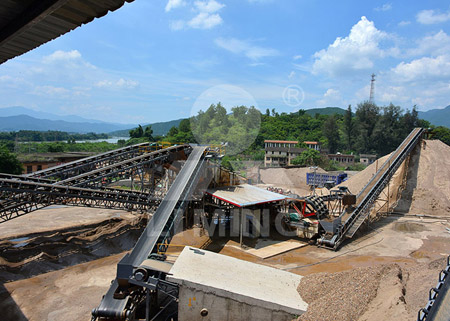
grinding process in iron ore
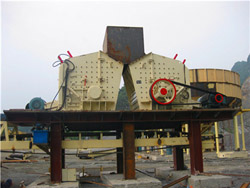
Comminution and classification technologies of iron ore
8.1. Introduction Hematite and magnetite iron ores are the most prominent raw materials for iron and steel production. Most of the high-grade hematite iron ores The grinding tests were performed feeding a blend of 80% ore A (compact and harder) and 20% ore B (porous and brittle). The variable parameters Development of a Novel Grinding Process to Iron Ore
احصل على السعر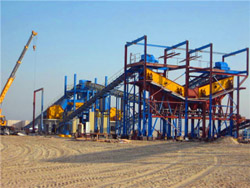
Research into the crushing and grinding processes of iron ore with
Technological cycle of iron ore crushing and grinding under production conditions is possible only in terms of mechanical load being rather labour-consuming and energy Development of a Novel Grinding Process to Iron Ore Pelletizing through HPGR Milling in Closed Circuit Mining Metallurgy & Exploration Authors: Anderson Denadai Thomazini Eduardo Poltronieri...(PDF) Development of a Novel Grinding Process to Iron
احصل على السعر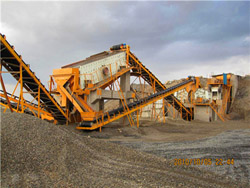
(PDF) Iron Ore Pelletizing Process: An Overview
Iron ore pellet making process involves balling of green mix (containing iron ore fines, binder, limestone and coke) using rotating disk or drum to produce green pellets.grinding routes to minimize the impact on the resources and to increase the pellet competitiveness. A leaner preparation process was conceptualized based only on the Development of a Novel Grinding Process to Iron Ore Pelletizing
احصل على السعر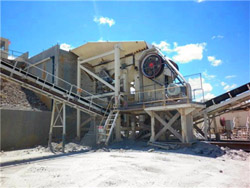
Development of a Novel Grinding Process to Iron Ore Pelletizing
The present study considers a novel milling process applying only HPGR as a re-regrind stage after concentration. The amount of successive ground product cess parameters during grinding of hard banded hematite quartzite iron ore (BHQ) in HPGR. 2 Materials and Methods A banded iron ore (BHQ) sample from Odisha was used in this study. The bulk sample was crushed to below 20 mm size and was thoroughly mixed, and representative sample was collected by standard conning and quartering method.Potential of High-Pressure Grinding Roll (HPGR) for Size
احصل على السعر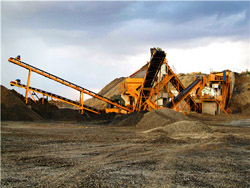
Methods of Ore Pretreatment for Comminution
The machine could process ore up to 10 th −1 (3–10 th −1), depending on the pulse energy, PSD, and density of the ore. The PSDs of the tested ores were 22.4 Effect of thermal treatment via furnace on Iron ores obtained from different sources differ in their chemical and physical properties. These variations make the process of grinding a difficult task. The work carried out in this context focuses on three different samples of iron ore, viz., high silica high alumina, low silica high alumina, and low silica low alumina. The grinding Estimation of Grinding Time for Desired Particle Size Distribution
احصل على السعر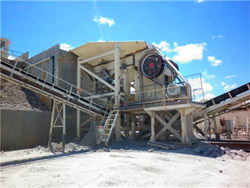
Research of iron ore grinding in a vertical-roller-mill
Vertical-roller-mills (VRM) are an energy-efficient alternative to conventional grinding technology. One reason is the dry in-bed grinding principle. Results of extensive test works with two types of magnetite iron ores in a Loesche VRM are presented here. Within these test works, mill parameters like grinding pressure, Vanadiferous titanomagnetite (VTM) ore is a typical polymetallic paragenic mineral, which is composed of a mixture of several of a variety of valuable metal elements—such as iron, titanium, vanadium, calcium, aluminum, etc. [1,2]—and has extremely high strategic and comprehensive utilization value [3,4].In China, VTM ore is Metals Free Full-Text Study on the Grinding Kinetics and MDPI
احصل على السعر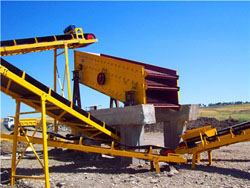
Research of iron ore grinding in a vertical-roller-mill
Semantic Scholar extracted view of "Research of iron ore grinding in a vertical-roller-mill" by Mathis Reichert et al. Skip to search form Skip to main content Skip to account menu. Semantic and the breakage of coals by the ball-and-race mill or roller mill is an energy-intensive process. Grinding phenomena in mill of The mixing speed and temperature were the same as those in the gold powder leaching experiment. In the dry grinding process, 50 g of roasted gold concentrate was ground in a planetary mill for 5 min. The wet grinding process was performed in a ball mill for 10 min. The particle size distributions of the wet and dry milled ore are shown in Use of dry grinding process to increase the leaching of gold from
احصل على السعر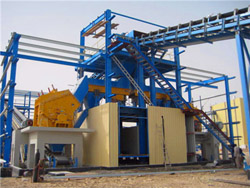
Research of iron ore grinding in a vertical-roller-mill
The ores were already pre-crushed and had a particle size of +0 to 10 mm. In preparation of the grinding tests the materials were homogenised to ensure constant feed material properties. 2.3. Design of experiments. A systematic approach is used for the analysis of the process of ore grinding in VRM’s.The process of iron ore reduction is to make the large blocks of iron ore rocks small enough for the next ore grinding process, when large blocks are transfered from mines or quarries of iron ores. For usual condition, ore reduction contains primary crushing, secondary crushing and fine crushing. Engineering Department.Iron Ore Process PDF Iron Ore Mill (Grinding) Scribd
احصل على السعر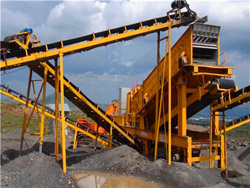
Beneficiation of Low-Grade Dilband Iron Ore by Reduction
This research is aimed at the up-gradation of indigenous Pakistani iron ore, i.e., Dilband iron ore (hematite), by utilizing common metallurgical processes. First, the magnetic properties of the ore were determined. Initially, the iron ore samples contained 34 wt. % Fe in addition to other gangue materials. Therefore, the ore was subjected to a 1. Introduction. Iron ore pellets are one of the significant sources of iron for iron and steel making due to their superior metallurgical performance, low energy consumption, and less emission of environmentally harmful dust and gases during the production process [1], [2], [3].The two primary raw materials for pellet production are Mechanism of magnetite iron ore concentrate morphology
احصل على السعر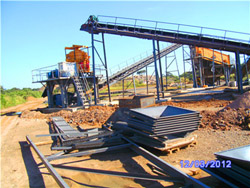
What Role does the Grinding Machine Play in Iron Beneficiation Process
Iron ore beneficiation is a crucial process in the extraction and refinement of iron ore resources. Among the various stages involved in this process, grinding equipment holds a pivotal position.Washing of iron ore fines and slime (10% and 25% w/v, slurry concentrations) with two types of surface-active agents (sodium humate (synthesized) and AD 200 (commercial)) at varying concentrations at pH 8 was conducted for ascertaining the efficacy of dispersants in beneficiating the low-grade iron ores. The beneficiation Upgradation of Iron Ore Fines and Slime by Selective Hindawi
احصل على السعر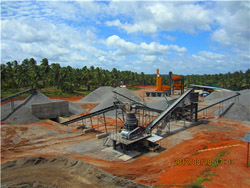
Reduction of Fragment Size from Mining to Mineral Processing: A
2.1 Energy. Rock drilling, blasting, and comminution (crushing and grinding) consume a vast amount of energy in hard rock mines. As mentioned in Sect. 1, statistics from hard rock mines indicates that drilling and blasting consumes 2% and comminution does 53% of the total energy input in the whole production chain from It has been estimated that grinding consumes up to 4% of global electrical energy and accounts for more than 50% of the total energy used in mining operations. In addition, more than 90% of the total energy supplied in beneficiation plants is dissipated as heat, kinetic energy, noise, and inefficient breakage of ores/raw material.Special Issue "Grinding Modeling and Energy Efficiency in Ore
احصل على السعر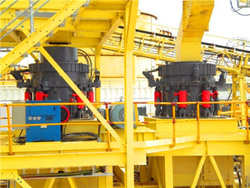
Development of a Novel Grinding Process to Iron Ore Pelletizing
The earliest industrial application of high pressure grinding rolls (HPGR) at comminution was in 1984 in the cement industry. Since then, the equipment has been widely applied in mining activities. Despite the rapid spread across the industry, several challenges are still present in the equipment’s application, especially considering the complex ore Iron ore tailings (IOTs) are a form of solid waste produced during the beneficiation process of iron ore concentrate. In this paper, iron recovery from IOTs was studied at different points during a process involving pre-concentration followed by direct reduction and magnetic separation. Then, slag-tailing concrete composite admixtures Minerals Free Full-Text Recovering Iron from Iron Ore Tailings
احصل على السعر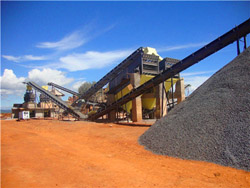
Process flow sheet for Pelletization using dry grinding process
Download scientific diagram Process flow sheet for Pelletization using dry grinding process from publication: Iron Ore Pelletization Technology and its Environmental Impact Assessment in EasternThe present work has identified an entirely new process circuit covering the crushing and grinding, and iron ore beneficiation, building on the above developments. In principle, the approach is vastly simpler, more environmentally sustainable, and cost effective than the conventional circuit, hence may have very significant implications Transforming iron ore processing ScienceDirect
احصل على السعر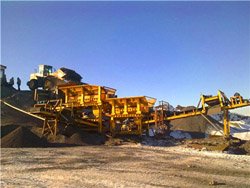
(PDF) Iron Ore Concentrate Particle Size Controlling Through
The moisture and, consequently, balling control have a starting point at the comminution process, where several types of equipment is applied in iron ore operations. The comminution process based
احصل على السعر