
how to control residue in ball mill in cement plant
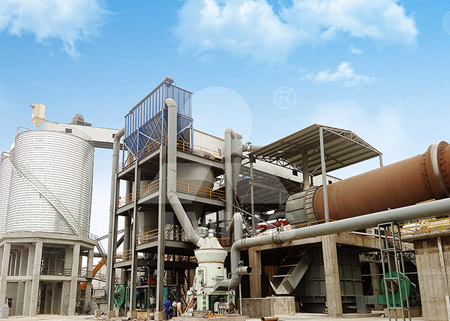
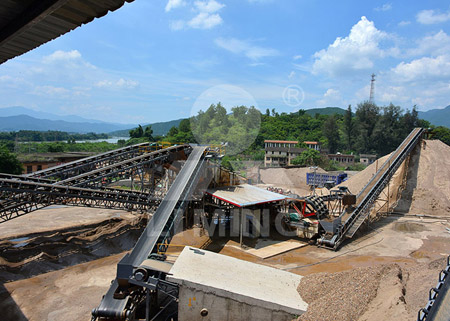
how to control residue in ball mill in cement plant
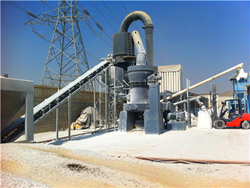
BALL MILLS Ball mill optimisation holzinger
Ball mill optimisation As grinding accounts for a sizeable share in a cement plant’s power consumption, optimisation of grinding equipment such as ball mills can The control law obtained in Equation (15) is introduced into the cement ball mill grinding process to optimise the plant for the desired product quality Predictive Controller Design for a Cement Ball Mill
احصل على السعر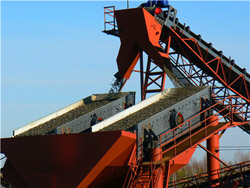
Optimization of Cement Grinding Operation in
1. Optimization of the Cement Ball Mill Operation Optimization addresses the grinding process, maintenance and product quality. The objective is to achieve a more efficient operation and increase the production rate as Ramasamy et al. (2005) used MPC to control a ball mill grinding circuit composed of fresh feed, hydrocyclone, ball mill, sump and pump. The controlled Control of a closed dry grinding circuit with ball mills using
احصل على السعر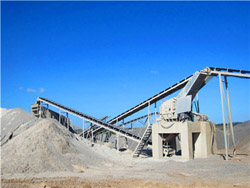
Energy and exergy analyses for a cement ball mill of a new
In this work, the energy and exergy analyses of a cement ball mill (CBM) were performed and some measurements were carried out in an existing CBM in a It could also be inferred that residue is inversely related to Blaine or fineness. 15 rpm mill speed is near the critical mill speed, thus Blaine is minimum whereas residue is higher at 16% (Fig. 12).a) Cement ball mill view, b) Cement mill sketch.
احصل على السعر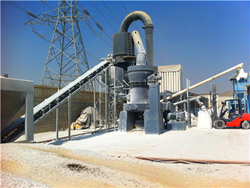
Effects of Mill Speed and Air Classifier Speed on
Mill speed and air classifier speed were the investigated parameters for the closed cycle mill. Almost six speed level are used in the closed cycle mill are 750, 800, One of the most critical variables in the cement ball mills is ventilation. A mixture of hot and recycled air would deliver and dry the powder in a cement ball mill as Ventilation Prediction for an Industrial Cement Raw Ball
احصل على السعر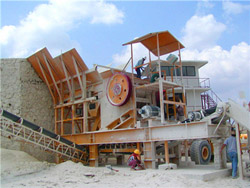
Coal Grinding Cement Plant Optimization
Ball Mill: Single chamber ball mills (with classifying liners and dam ring) with drying chamber and static or dynamic separator are commonly existing for coal grinding in cement plant for one or more kilns as per capacity. Ball mill is a cylinder rotating at about 70-80% of critical speed on two trunnions in white metal bearings or slide shoeVarious studies lead to the conclusion that toxic pollutants in cement dust affect the growth of plants (Iqbal and Shafig 2001).Dust from cement factories may have an effect by forming toxic solutions which come from water reacting with alkaline dust or through a decrease in light (Manning 1971).Mercury was found in the leaves of Weigela Cement Dust Pollution and Environment SpringerLink
احصل على السعر
cement blaine and residue on 45 micron control? Page 1 of 1
re cement blaine and residue on 45 micron control? Since both are a measure of particle size, residue is normally linked to Blaine. But not always. It depends on the particle size distribution of the cement and this is driven by several things including mill design, ball charge (or grinding pressure in a roller mill), clinker hardness, gypsumNowadays, ball mills are widely used in cement plants to grind clinker and gypsum to produce cement. The research focuses on the mill speed as well as air classifier speed effect on the two(PDF) Effects of Mill Speed and Air Classifier Speed on
احصل على السعر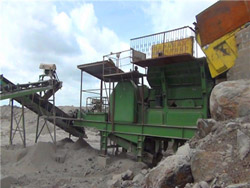
PROCESS DIAGNOSTIC STUDIES FOR CEMENT MILL
A 1.5 mio t/a cement plant is having a closed circuit ball mill for cement grinding: The mill has been operating with satisfactory performance in-terms of system availability and output, however power consumption was on higher side. 3.1 System Description Mill Rated capacity 150 t/h OPC at 2800 blaine I chamber linersMeng, Q., Wang, Y., Xu, F. & Shi, X. Control strategy of cement mill based on bang-bang and fuzzy PID self-tuning. in 2015 IEEE International Conference on Cyber Technology in Automation, ControlModeling of energy consumption factors for an industrial cement
احصل على السعر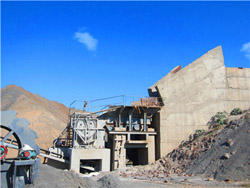
Coal utilisation in the cement and concrete industries
Abstract: The utilisation of coal in the cement and concrete industries takes three basic forms: 1. As a fuel in the production of cement clinker, 2. Ash produced by burning coal in power stations is used as a component in cement rotary kiln feeds, 3. Ash produced by burning coal in power stations is used as a mineral additive in concrete mixes.The energy consumption of the total grinding plant can be reduced by 20–30 % for cement clinker and 30–40 % for other raw materials. The overall grinding circuit efficiency and stability are improved. The maintenance cost of the ball mill is reduced as the lifetime of grinding media and partition grates is extended. 2.5.Energy-Efficient Technologies in Cement Grinding IntechOpen
احصل على السعر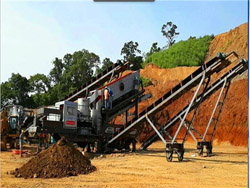
Cements ground in the vertical roller mill fulfil the quality
This study investigated a mathematical model for an industrial-scale vertical roller mill(VRM) at the Ilam Cement Plant in Iran. The model was calibrated using the initial survey's data, and theZhang et al. (2020) controlled the cement combined grinding mill, consisting of a roller press, cyclone, separator and ball mill. The input variable was the ball mill's current, and the controlled variable was the circulating fan's rotating speed. Data were collected every 10 seconds, which reduced the impact of time delay.Control of a closed dry grinding circuit with ball mills using
احصل على السعر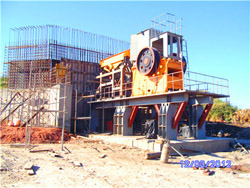
Full article: An overview of alternative raw materials used in cement
Raw materials chemistry. Cement manufacture requires a source of calcium, such as CaCO 3 or CaMg (CO 3) 2, which comprises almost 80–90% of the total and the rest is iron oxide (Fe 2 O 3, Fe 3 O 4), quartz (SiO 2), and clay/bauxite (Al-silicates) (Aïtcin and Flatt Citation 2015; Hewlett Citation 2003; Peray and Waddell Citation 1986).Traces of Na 2 O, K 2 O, To maintain a vertical raw mill in a cement plant, the following steps can be taken: Regular lubrication: Lubricate the various parts of the mill regularly to reduce friction and wear. MonitoringHow to maintain vertical raw mill in cement plant? LinkedIn
احصل على السعر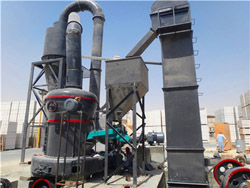
Clinkerization an overview ScienceDirect Topics
Grinding of cement clinker together with additives to control the properties of the cement is done in ball mills, roller mills, or roller presses. Coarse material is separated in a classifier to be returned for additional grinding. Power consumption for grinding depends strongly on the fineness required for the final product and the use ofA ball mill is a type of grinder widely utilized in the process of mechanochemical catalytic degradation. It consists of one or more rotating cylinders partially filled with grinding balls (made(PDF) Grinding in Ball Mills: Modeling and Process Control
احصل على السعر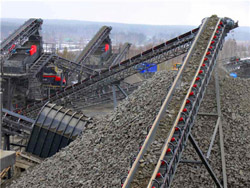
Optimization of Cement Grinding Operation in Ball Mills
The optimization of this process would yield substantial benefits in terms of energy savings and capacity increase. 1. Optimization of the Cement Ball Mill Operation. Optimization addresses the grinding process, maintenance and product quality. The objective is to achieve a more efficient operation and increase the production rate as well asTypically, RDF can replace up to 15-20% of primary fossil fuels used in cement plants. However, the current thermal substitution rate (TSR) or the rate of co-processing wastes in India ranges(PDF) Municipal Solid Waste Co-processing in Cement
احصل على السعر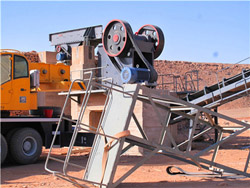
Optimizing Raw Mills Performance PDF Mill (Grinding) Cement
Optimizing Raw Mills Performance ; the. Materials WAY Introduction: Raw milling is one of the most important and integral component of cement production process; it is the stage which produces the most important intermediate product i.e. Raw Meal which is critical not only from cost point of view (Fuel / Electricity consumption) but Ball mill control -Automatic start-up control In most cement plants, start up of a mill is conducted through a series of manual operations on the part of an operator. The operator switches on the mill, starts the mill feed and,after ascertaining that the mill load becomes stable,changes the control mode to the constant-value feedbackOptimization of Cement Manufacturing Process ScienceDirect
احصل على السعر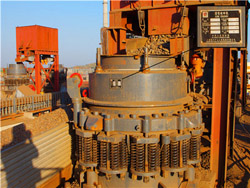
Best energy consumption International Cement Review
Plant 3 Vertical mill (kWh/t cement) CPJ 35. 30.8. 29.8. 30.4. CPJ 45. 32.5. has been a minor trend back to ball mills. This is most evident for petcoke grinding, where the demand for very low residues, and the very hard and sometimes abrasive nature of high-sulphur cokes has resulted in ball mill selection. In the key area of
احصل على السعر