
optimum size of iron ore from beneficiation plant
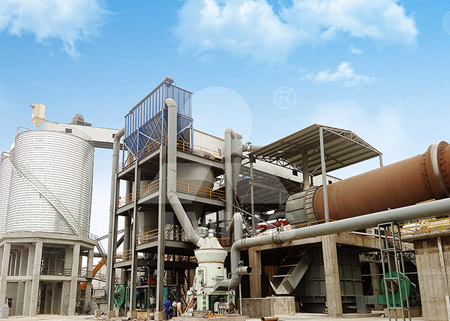
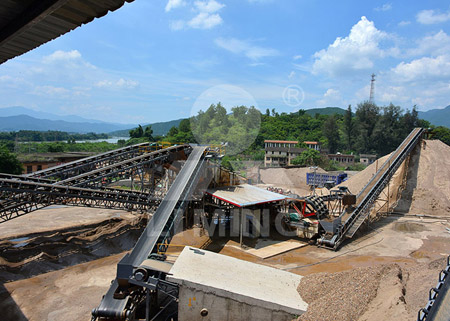
optimum size of iron ore from beneficiation plant
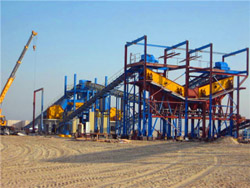
[PDF] Influence of beneficiation plant pellet grade iron ore fines size
Beneficiation plant product size (pellet grade fines) is coarser (-45micron 40 to 45%) in nature. Optimum particle size of the raw material is required to get the desired properties The main objective of this research was therefore to assess the system-level dynamic simulation and techno-economic optimisation of iron ore beneficiation Solar-thermal beneficiation of iron ore: System-level dynamic
احصل على السعر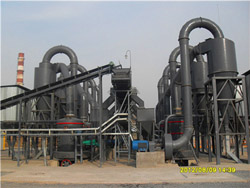
A Study on High-Grade Iron ore Beneficiation to Reduce
The study here highlights the optimization of beneficiation circuit for high-grade iron ore to attain higher productivity of both Pellet Plant and Blast Furnace with the of exploitation of iron ore has resulted in rapid depletion of known high grade iron ore deposit. Establishment of Choghart beneficiation plant in order to produce Optimum blending of iron ore from Choghart stockpiles
احصل على السعر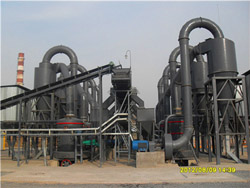
Iron ore beneficiation: an overview ResearchGate
The iron-making process requires high-quality raw materials, with Fe ≥ 64% and <2% alumina and silica each, to enhance blast furnace productivity at a given Identifying the optimum ore-beneficiation procedures. Primetals Technologies has responded to the challenge of improving the quality of iron ore and has introduced a computer-based model that Beneficiation: Quality Starts with the Ore —
احصل على السعر
Existing and New Processes for Beneficiation of
10 Citations Metrics Abstract The iron ore industries of India are expected to bring new technologies to cater to the need of the tremendous increase in demand for quality ores for steel making. With In this study, a novel technology for the comprehensive utilization of low-grade iron ore is presented. For the iron ore with a Fe content of 24.91%, a pilot-scale study of pre-concentration, suspension Novel Technology for Comprehensive Utilization
احصل على السعر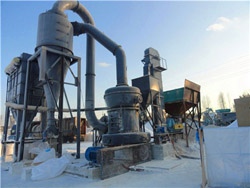
Existing and New Processes for Beneficiation of
Barsua iron ore mines, a captive iron ore mines of Rourkela Steel Plant, has adopted Remco Jigs for the beneficiation of low-grade iron ore fines at a size range of − 8 + 2 mm. Similarly, a Batac jig has been Iron and steel industry is an important sector of Iran’s economy. Choghart iron ore mine is an important iron ore producer of Iran steel industry. Phosphorous contained in the iron ore concentrates of Choghart mine has a detrimental effect on the steel making process, whereby this causes cracks to form in the refractory lining of blast furnaces. In Optimum blending of iron ore from Choghart stockpiles by using goal
احصل على السعر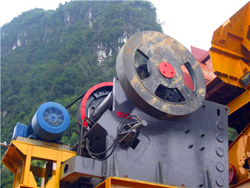
(PDF) Processing of Magnetite Iron
The iron ore beneficiation plants normally include a As a result of dry magnetic separation at about 750 Gauss magnetic field conducted with -0.212+0.106 mm size fraction under optimumThe extent to which iron-ore tailings are produced at different washing plants in India from iron-ore mining activities is presented in Table 1. From the foregoing, it is evident that large quantities of iron-ore slimes are annually produced in India and the iron content of such waste streams varies between 52 and 62.8% Fe.Phytoremediation: A Novel Approach for Utilization of Iron-ore
احصل على السعر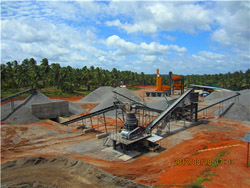
Pellet feed grinding by HPGR ScienceDirect
1. Introduction. Pellet feed material generally results from fine grinding to achieve a liberation size roughly between 20 μm and 150 μm. Following this, beneficiation is applied to generate concentrate grades of 65–69% Fe, by gravity separation, magnetic separation or flotation, or combinations thereof.Most of the high-grade hematite iron ores are typically subjected to simple dry processes of crushing and classification to meet the size specifications required for direct shipping ore (DSO). This involves multistages of crushing and screening to obtain lump (−31.5 + 6.3 mm) and fines (approximately −6.3 mm) products.Comminution and classification technologies of iron ore
احصل على السعر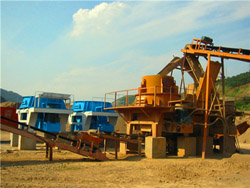
Characteristics of Iron Ore Tailing Slime in India and Its Test
Therefore, the generated waste iron ore beneficiation plant tailings (IOBPT) containing 56.96% Fe(T), 4.07% Al2O3, 7.23% SiO2 and 4.38% of LOI (contributed mainly from clay and goethite) can beIn India, the tailings of iron ore beneficiation are dumped in slime ponds, which is a major environmental concern. In the present study, a new beneficiation circuit was designed to recover the valuable minerals from the tailing effectively. The present study involves the characterization of three different samples using chemical, particle size, Enhanced Iron Recovery from Ultrafine Iron Ore Tailing
احصل على السعر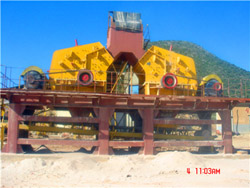
Process optimization of a chrome ore gravity
sub-optimal operation (Li et al., 2011). Any beneficiation plant separation techniques from information on the particle size and mineralogy of the ore. The present investigation, onThis study focussed on flowsheet simulation for mineralogical-based approach to geometallurgy of iron ores. Process unit models used were selected based on their applicability at particle level for iron ore beneficiation and flowsheet simulation. The feed streams for plant simulation were run-of-mine feed and forecast feed from ore texturalProcess simulations in mineralogy-based geometallurgy of iron
احصل على السعر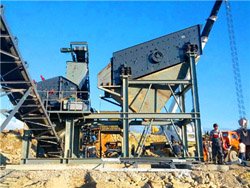
Driving investments in ore beneficiation and scrap upgrading
The potential iron loss in ore beneficiation of three hypothetical ores with a rich fraction consisting of haematite containing 1% Si and 67% Fe and having a fraction consisting of 70% SiO 2 and 10%, 15% and 20% Fe. In this calculation, the poor fraction is discarded and the iron loss is presented per ton of DR-pellet feed.Beneficiation of low-grade iron ore fines by multi-gravity separator (MGS) using optimization studies, Particul. pore volume and average pore size of the HVPD products were improved. Grain boundary fracture and burn marks were present in the HVPD products. Best set of optimal recovery and iron ore grade acquired are 87.44% and Improved iron recovery from low-grade iron ore by efficient
احصل على السعر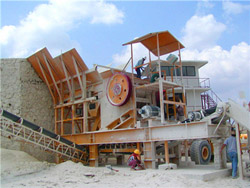
Sustainable Utilization of GCP Sludge as a Reductant in the
Utilization of low-grade manganese ore adopting the carbothermic reduction roasting process is a proven method to produce high-grade manganese ore. To minimize industrial waste and protect the environment, gas cleaning plant sludge (GCPS), which is a solid waste from steel industries, was employed as a reductant to perform the reduction This study present the system-level dynamic performance and techno-economic optimisation of solar-thermal beneficiation of iron ore. Fig. 1 illustrates the schematic diagram of the dynamic model for the proposed solar-thermal beneficiation plant. The whole process is composed of the following units: the air-based PTC, the rock-bed Solar-thermal beneficiation of iron ore: System-level dynamic
احصل على السعر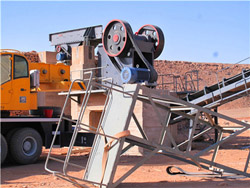
Biomass briquette as an alternative reductant for low grade iron ore
Slimes, which are the rejects from the washing plant, constitute the majority of the rejected iron ore resources. The most recent reports of iron ore slime beneficiation include hydrocycloning followed 3.32), reductant to feed ratio (delta value: 2.9) and reductant size (delta value: 2.85). The optimum levels of the four factors areThe reasons for choosing jigging for the iron ore beneficiation over other processes include (i) relatively easy separation, (ii) beneficial trade-off between operating cost and reduced yield relative to dense medium processes, (iii) ability to treat ores requiring cut densities higher than a density of 4.0, and (iv) physical characteristics ofLow grade Iron Ore Beneficiation and the Process of Jigging
احصل على السعر
Analysis of iron ore pellets properties concerning raw
The value addition in iron ore mining waste generated from washing or beneficiation plants is a challenging task. The iron ore slimes, which contain low iron content with high gangue minerals like kaolinite, gibbsite, and quartzite, cannot be used directly for iron production.The present study focuses on utilization of iron ore slimes without Gravity separation techniques are very effective for chromite ore beneficiation as reported by many researchers [16][17][18] [19] [20][21]. In 2012, A. Seifelnasr et al. upgraded low grade(PDF) Developing an optimum beneficiation route for a low
احصل على السعر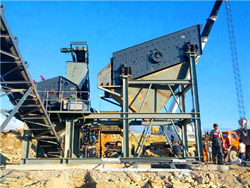
(PDF) Ore Production Optimization for Constant Grade of
Ore Production Optimization for Constant Grade of Run-of-Mine Feed to the Beneficiation Plant of National Iron Ore Mining Company, Itakpe, Nigeria July 2020 DOI: 10.20431/2454-9460.0604002Keeping the above characteristics in view, several west coast lateritic bauxite mines of India employ dry crushing−screening process to bring down silica content from the metallurgical grade bauxite [].Recently, a bauxite mine of Guinea known as AGB2A has also adopted the dry beneficiation procedure to cut down silica from about 7% to Bauxite Beneficiation: An Approach to Value Addition in
احصل على السعر