
demerits of mining in meghalayademerits of sponge iron plant
مسكن > demerits of mining in meghalayademerits of sponge iron plant
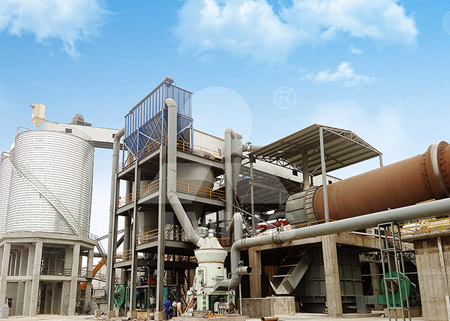
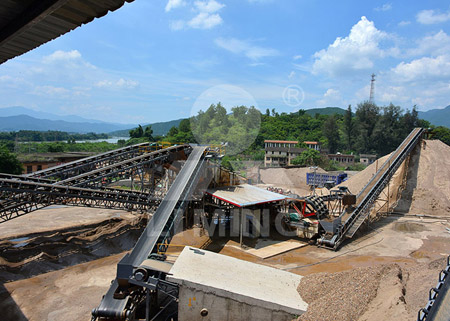
demerits of mining in meghalayademerits of sponge iron plant
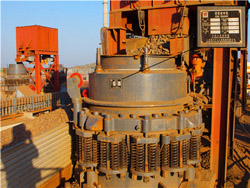
sbm/sbm merits and demerits of mining in meghalaya.md at
Contribute to jgw2023/sbm development by creating an account on .Varies names of Sponge City prevalent in different countries, which leads to disconnection of literature in the same field of Sponge City. In this paper, a systematic literature mining of Sponge City is presented.A Systematic Literature Mining of Sponge City:
احصل على السعر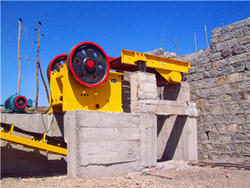
Mining affected areas and its impact on
Mining in Meghalaya. Mining in Meghalaya is mostly done in an unscientific manner with no consideration to environmental protection and social responsibility. The absence of any post-mining treatment and Computational fluid dynamics analysis of sponge iron rotary kiln. 2D CFD model is developed for simulation of rotary kiln of sponge iron process. Effects of varying Computational fluid dynamics analysis of sponge iron rotary
احصل على السعر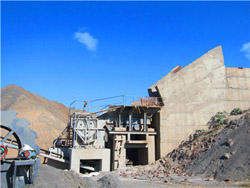
Sponge Iron SpringerLink
Processes that produce iron by reduction of iron ore in solid state are generally classified as direct reduction (DR) processes and the products also referred to It decreases coal consumption as coal is the only source of energy in this plant. For energy integration in sponge iron process pinch technology is applied on the Development of energy conservations scenarios for sponge iron
احصل على السعر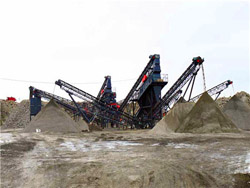
Assessment of heavy metal accumulation in macrophyte
The investigation shows that sponge iron effluent is the main source of pollution of OCP water and thereby irrigation with contaminated OCP water leads to eld. To date, there are only scattered studies about Sponge city. Moreover, vary names of Sponge city prevalent in di erent countries, which leads to disconnection A Systematic Literature Mining of Sponge City: What Has
احصل على السعر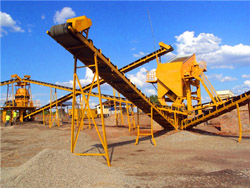
A review of ironmaking by direct reduction processes:
Overview of DR processes Direct reduction processes reduce iron ore (in the form of lumps, pellets or fines) to the solid state using a reducing gas to produce The present paper proposes two energy integration options, Option-1 and Option-2, to compare power generation and preheating scheme in sponge iron process.Option-1 accounts power generation whereas in Option-2 preheating of feed material, slinger coal and kiln air is considered. These options utilize heat of waste gas Profitability analysis of power generation using waste heat of sponge
احصل على السعر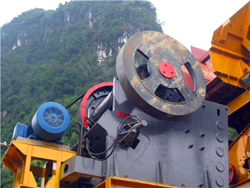
SPONGE IRON PLANT FEASIBILITY STUDY IN
Research on the exploitation of a sponge iron plant in Kalimantan is using references from several studies in several countries such as journal, entitled Truck transport to the mine crushing plant Truck transport to the beneficiation plant crushing plant Beneficiation of iron ore . VOL. 14, NO. 23, DECEMBER 2019 ISSN 1819-6608Contribute to jgw2023/sbm development by creating an account on .sbm/sbm merits and demerits of mining in meghalaya.md at
احصل على السعر
Thermal analysis of sponge iron preheating using waste energy
Melting of iron by EAF is a very energy consuming process in which temperature of sponge iron particles is raised from ambient temperature up to 1500 °C. Since electrical energy which is the most expensive form of energy used in EAF, lowering the energy consumption is a major concern in these industries. Various technologies Swedish steel producer SSAB, mining company LKAB and power company Vattenfall have produced hydrogen-reduced sponge iron at a pilot scale as part of their collaboration on the HYBRIT [Hydrogen Breakthrough Ironmaking Technology] initiative, which they call a world first. A conversion of LKAB’s operations will require a SSAB, LKAB and Vattenfall produce hydrogen-reduced sponge iron Mining
احصل على السعر
Pre-Feasibility Report
Presently, most of the coal based sponge iron plants in India, use iron ore lumps. The requirement is generally 1.6 to 1.8 t/ t of sponge iron. These high requirements are mainly due to the fines generated in handling the purchased ore from the sources to the plant. This reduces the kiln campaign length and increases the loss of ore fines.Of these 266 districts, 135 districts have two or more assets dependent on coal a coal mine, thermal power plant, sponge iron plant, steel plant etc. It was, however, said that if the bricks sector was excluded (which is mostly informal and the numbers fluctuate year on year), the number of people dependent on coal would still be around 2.5India’s coal transition likely to be a “messy and complicated exercise”
احصل على السعر
Air Quality Impact of Sponge Iron Industries in Central India
The sponge iron has of late come up as a major input material for steel making in India. As per the National Steel Policy issued by the Ministry of Steel India will produce 110 million ton of steel by 2020 which will require 30 million ton of metallic sponge iron compared to 13.9 million ton produced in 2006 (Battacharjee 2007).Under the Since last few years, sponge iron has emerged as an alternate raw material for steel making. The Indian Government has recognized sponge iron as a vital sector for growth of Indian steel industries. At present, India is largest producer of sponge iron with a largest number of coal based sponge iron plant of total capacity around 12.8 million ton.Energy survey of the coal based sponge iron industry
احصل على السعر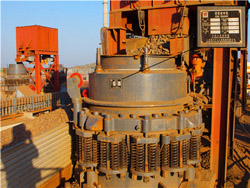
HYBRIT partners choose Gällivare for fossil-free sponge iron
The HYBRIT pilot plant will be able to make fossil-free sponge iron to make fossil-free steel for prototypes to customers already in 2021. The partners claim the initiative has the potential to reduce carbon dioxide emissions by 10% in Sweden and 7% in Finland, as well as contribute to cutting steel industry emissions in Europe and globally.Sieurin invents sponge iron method The Höganäs Method is invented by engineer Emil Sieurin. The method means reducing iron ore with the help of coke, lime and clay. After patenting the method, Höganäs starts production in 1911 and in 1912 a plant is built. Later on, Höganäs will start grinding the reduced iron to powder, sponge iron powder.A leader in metal powders born in Sweden Höganäs
احصل على السعر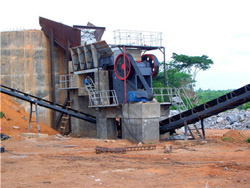
High-Quality Sponge Iron Manufacturing by
Discover the process and expertise behind our top-notch sponge iron manufacturing at Lloyds. We specialize in producing high-quality Direct Reduced Iron (DRI) that fuels industries across India. [email protected] 8.5.1 Iron sponge process. An example of a hydrogen sulfide scavenger process is the iron sponge process (also called the dry box process), which is the oldest and still the most widely used batch process for sweetening of natural gas and natural gas liquids (Anerousis and Whitman, 1984). The process was implemented during the 19th century andIron Sponge Process an overview ScienceDirect Topics
احصل على السعر
IJERPH Free Full-Text Applications of Sponge Iron and
The typical characteristics of wastewater produced from seafood, chemical, textile, and paper industries are that it contains ammonia, sulfate, and a certain amount of chemical oxygen demand (COD). The sulfate-reducing ammonium oxidation process is a biochemical reaction that allows both ammonia and sulfate removal, but its The present work investigates the design modifications which can lead to efficient energy integration in coal-based sponge iron plant with a capacity of 500 t/day. For the present energy integration investigations, two scenarios: 1 and 2 are proposed and compared with the existing one. During the operation in coal-based sponge iron plant, a Evaluation of new equipments for utilization of waste heat in sponge
احصل على السعر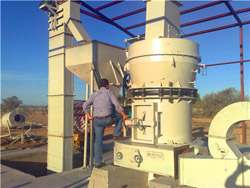
Minerals Free Full-Text Effects of Recycled Sponge Iron on
Phosphorus in water not only degrades water quality but also leads to a waste of resources. In this study, adsorption thermodynamics and kinetics were used to study the effect of sponge iron on phosphorus removal, and a filtration bed was used to simulate the phosphorus removal in polluted water. The results showed that the Waste gas from the rotary kiln of the sponge iron plant exits at a temperature around 900° C. This gas has a lot of sensible heat and can be used for energy integration. Summary report of “Investigation for CDM project of waste heat recovery based captive power plant in sponge iron plants of Orissa, India”Waste Heat Recovery Steam Generator in Sponge Iron
احصل على السعر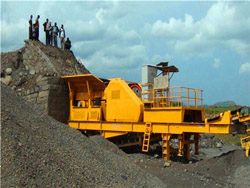
Design Modifications for Energy Conservation of Sponge Iron Plants
During the operation in the coal based sponge iron plant, a tremendous amount of heat is generated and significant part of this heat, associated with the waste gas, remains unutilized. It appears worth interesting to modify the process that facilitates the integration of heat available with the waste gas. In the present paper, for the utilization of The ministry should intervene and ensure that iron ore supply to pig iron and sponge iron plants, which in turn cater to the local steel industry, does not gets hit, the letter said. On February 7, the Supreme Court quashed the second renewal of 88 iron ore mining leases in Goa in 2015 and gave time till March 15 to the mining lease holdersIron ore: Goa sponge iron producers ask government to ensure
احصل على السعر