
tube ball mill for grinding iron ore fines
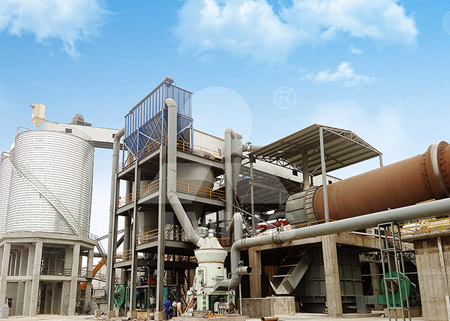
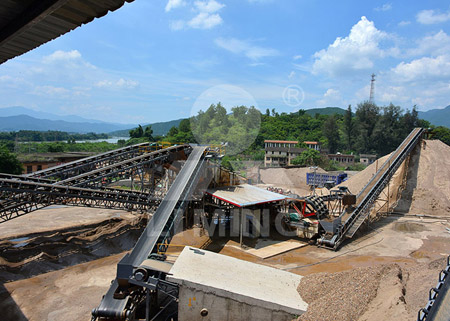
tube ball mill for grinding iron ore fines
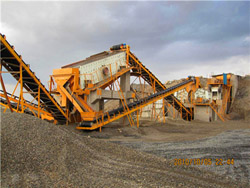
Optimization of Solids Concentration in Iron Ore
The paper demonstrates the application of this methodology to optimize solids concentration in ball milling of an iron ore Four different laboratory ball mills and stirred mills have been tested to grind seven ore samples with feed sizes ranging from 3.35 mm to 150 μm. A case study on full Fine grinding in a horizontal ball mill ScienceDirect
احصل على السعر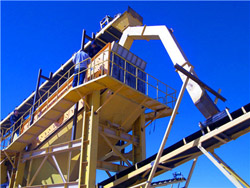
Vertical mill simulation applied to iron ores ScienceDirect
The application of vertical mills in regrind circuits is consolidated. This type of mill is now attracting interest in primary grinding applications, due to its higher The iron ore blend takes RT of 13 min when grounded in the BBM for 250% circulating load with 80% passing particle size of 56 µm. The blend iron ore sample Investigation on Iron Ore Grinding based on Particle Size Distribution
احصل على السعر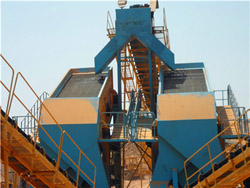
Addition of pebbles to a ball-mill to improve grinding
Ball-mills are used widely for secondary grinding. Loveday (2010) reported on laboratory tests in which small pebbles (7–25 mm) were used in various proportions 2.2.2. Ball milling of iron ores In this work, a dry ball milling process was conducted to pretreat Indian hematite ore fines. The grinding tests of the iron ore fines Grate-kiln pelletization of Indian hematite fines and its
احصل على السعر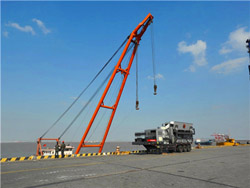
Friction and wear of liner and grinding ball in iron ore ball mill
Some were severely worn and unrounded by iron ore from Anshan, China, during grinding operation in the vertical grinding mill (VTM-1500, TON Outotec). Their Some Current Sites and Details of Fine Grinding in Ball Mills (concentrate re-grind) Mill Dimensions Media Site, Company Application Dia. (m) Length (m) Type NOTICE: This is the author’s version of a work that was
احصل على السعر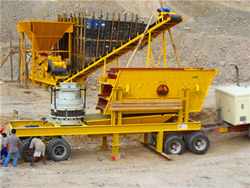
Investigation on Iron Ore Grinding based on Particle Size Distribution
The feed samples of X, Y, and Z iron ores were ground in the BBM (ball mill refers to a BBM of size 300 mm × 300 mm with smooth liners) to identify the PSD, BWI, and RT of each ore. Grinding experiments were conducted according to Bond’s standard test procedure [].For each iron ore sample, the RT taken to produce 250% circulating Due to the presence of gangue minerals in iron ore, the feed of hydrocyclone in the grinding circuit is a mixture of particles with different densities and sizes. This method had a minimal effect on the rate production of fines (−75 µm) and makes composite secondary milling even more attractive, for reducing the cost of ballsThe first attempt of applying ceramic balls in industrial tumbling mill
احصل على السعر
Comparing strategies for grinding itabirite iron ores in
The crushing-ball milling circuit specific energy was estimated on the basis of the Bond equation and the relevant Bond work indices (Table 4), with the crushing energy given from the SAG/AG F80 to a nominal product with P80 of 8.0 mm being added to the ball mill energy from F80 of 8.0 mm to the actual P80 of the pilot test, given either by theIn this case, the mill charge included both coarse ore fragments and steel balls. Two ore samples were characterized, and bench-scale grinding tests were carried out in laboratory mills 30 and 58(PDF) DEVELOPMENT OF A LABORATORY TEST TO DESIGN VERTICAL STIRRED MILLS
احصل على السعر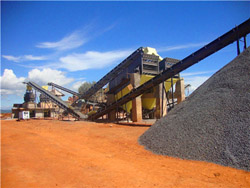
Developments in iron ore comminution and classification
The Zourerat iron ore mine has two 1.7 m diameter × 1.8 m wide HPGR units treating 1400 t/h each of aerofall mill pebbles. The feed is − 25 + 1.6 mm and has a ball mill work index of 12–14 kWh/t. The iron ore has low to moderate abrasion characteristics. Figure 8.21 shows the Zourerat iron ore flowsheet.X-MOL. Grinding iron ore concentrate by using HPGR and ball mills and their effects on pelletizing and reduction stages a pilot-scale study. Canadian Metallurgical Quarterly ( IF 0.9 ) Pub Date: ,DOI: 10.1080/00084433.2022.2052522. Seyed Hamzeh Amiri 1,Mohsen Izadi-Yazdan Abadi 2.Grinding iron ore concentrate by using HPGR and ball mills
احصل على السعر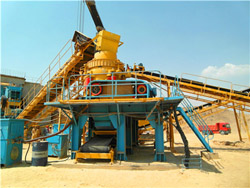
Reduction of Fragment Size from Mining to Mineral
A notable fact is that the energy efficiency of conventional milling is only about 1%, as mentioned in Sect. 1. An earlier experimental study indicated that about 80–90% of the energy input of a ball mill was used in heating the material (Schellinger 1951, 1952), and a recent study showed that over 75% of the electrical energy was used to Autogenous Mill 10 4.5 6400 353 18 Ball Mill 5 6.4 2600 126 21 Regrind Ball Mill 3.2 4.8 740 39 19 Tower Mill 2.5 2.5 520 12 42 IsaMill 1.3 3 1120 3 280 3 3) 23/m) Ball Mill Tower Mill IsaMill (m Power Intensity Media Size No. Balls / m Surface Area (kW/m (mm) 20 20 95,500 120 40 12 440,000 200 280 1 1,150,000,000 3600Fine Grinding as Enabling Technology The IsaMill
احصل على السعر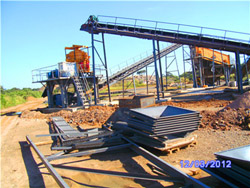
Size reduction performance evaluation of HPGR/ball mill and
A laboratory scale ball mill was used to conduct the grinding tests for PGE bearing chromite ore. The ball mill of 315 mm diameter and 305 mm length as shown in Fig. 3 (b) contained steel balls of a total weight of 28.124 kg. The characteristics of the mill used in the grinding studies and the test conditions are given in Table 1. The coningAbstract. The application of vertical mills in regrind circuits is consolidated. This type of mill is now attracting interest in primary grinding applications, due to its higher efficiency when compared to ball mills, which are usually used at this stage. In this study, a coarse sample of iron ore was tested in a pilot scale grinding circuitVertical mill simulation applied to iron ores ScienceDirect
احصل على السعر
THE EFFECTS OF PROCESS VARIABLES ON THE GRINDING OF IRON ORE
Grinding media-to-ore ratio of 3:0.5kg gave 21.00% fines, 79.00% coarse and mill filling is 3kg:1kg of media and iron ore liberating 15.00% fines and 85.00% coarse. Effect of Grinding Media-OreThe tests covered a range of slurry concentrations from 30 to 55 vol.% solid and fractional interstitial bed filling (U) from 0.3 to 1.75, at a fixed ball load (30% of mill volume) and 70% ofInvestigation of iron ores based on the bond grindability test
احصل على السعر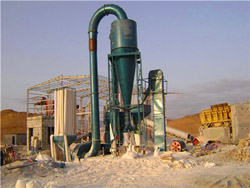
(PDF) A comparison of wear rates of ball mill
The performance of grinding media in a ball mill is also measured in terms of its wear rate. Abrasive ores such as gold and copper produce high wear rates of about 120µm/hr [74]. The wear ofThe present work applies the mechanistic mill model approach originally developed for ball mills by the UFRJ research group to the description of batch grinding in a pilot-scale vertical stirred mill. The model is used in its original form (Carvalho and Tavares, 2013) and predictions are compared to grinding of two materials at differentMechanistic modeling and simulation of a batch vertical stirred mill
احصل على السعر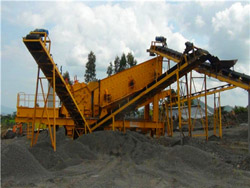
Development of a Novel Grinding Process to Iron Ore
2.1.2 Ore Blend Grinding at HPGR and Ball Mill. The ore blend was ground in a pilot-scale HPGR (1 m diameter × 0.32 m width) at a maximum feed rate of 50 t/h. The ground product was recirculated to the HPGR feeding hopper five or seven times, wherein every recirculation steps a sample was gathered for moisture and size distribution Ball Mill Power/Design Calculation Example #2. In Example No.1 it was determined that a 1400 HP wet grinding ball mill was required to grind 100 TPH of material with a Bond Work Index of 15 (guess what mineral type it is) from 80% passing ¼ inch to 80% passing 100 mesh in closed circuit. What is the size of an overflow discharge ball Ball Mill Design/Power Calculation 911 Metallurgist
احصل على السعر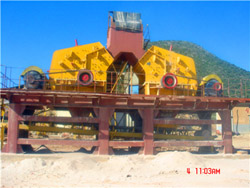
An energy based comparison of vertical roller mills and tumbling mills
The Institute of Mineral Processing at the Montanuniversitaet Leoben in cooperation with the company CEMTEC has developed a pilot scale, 200 mm table diameter, vertical roller mill for energy controlled laboratory tests.The mill provides the technical options to vary process parameters like air-flow, mass flow, grinding force and Introduction. As coarse grained, easily processed ore bodies are depleted, more disseminated, fine-grained ores are being treated. Adequate liberation of valuable components within a fine-grained ore is often only achieved once the particle size of the ore has been reduced to levels below the traditional ball mill cut-off of 45. μm.. To aid in the Fine grinding in a horizontal ball mill ScienceDirect
احصل على السعر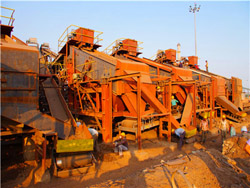
Investigation on the particle size and shape of iron ore
Abstract: An effect of a grinding method, that is ball mill and high pressure grinding rolls (HPGR), on the particle size, specific surface area and particle shape of an iron ore concentrate wasThe ball mill is a rotating cylindrical vessel with grinding media inside, which is responsible for breaking the ore particles. Grinding media play an important role in the comminution of mineral ores in these mills. This work reviews the application of balls in mineral processing as a function of the materials used to manufacture them and the A Review of the Grinding Media in Ball Mills for Mineral
احصل على السعر