
ball mill metal flakes
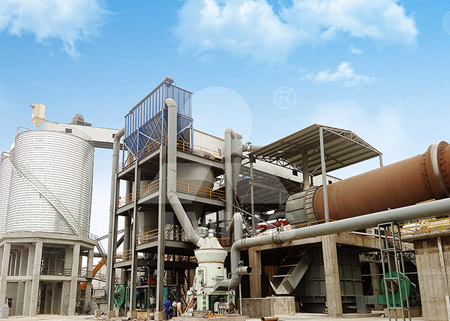
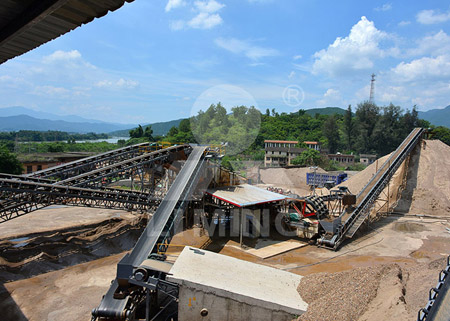
ball mill metal flakes

Metals Free Full-Text Progress of Flake Powder
The PM-based methods include high-energy ball milling [19,46,54], flake powder metallurgy [24,34], liquid-phase ball milling Ionics Micro/nano-Si flakes were obtained by a facile approach of reaction ball milling self-assembly, and then, a Si@C anode material with a carbon Reaction ball milling self-assembly derived micro/nano-Si flakes
احصل على السعر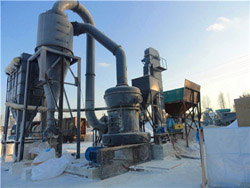
Ball Milling an overview ScienceDirect Topics
Ball milling, a shear-force dominant process where the particle size goes on reducing by impact and attrition mainly consists of metallic balls (generally Zirconia (ZrO 2) or steel For the preparation of graphene by ball milling, flake graphite is the primary raw material, aluminum powder is used as a grinding aid to help peel off the carbon layer, and steel sand of various particle Efficient preparation and characterization of
احصل على السعر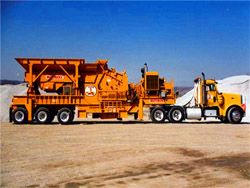
Ball milling induced borophene flakes fabrication RSC
Among so far studied techniques the potential of pure mechanical processes such as ball milling is not explored yet. Therefore, in this contribution, we PDF The High Energy (ball) Milling (HEM) technique has been found to be an efficient way to produce fine metal flakes. HEM follows the same principle Find, (PDF) Ductile Metal Flakes based on (Au), (Ag), (Al
احصل على السعر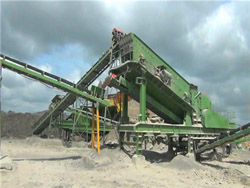
Ball Mill an overview ScienceDirect Topics
Ball mills are commonly used for crushing and grinding the materials into an extremely fine form. The ball mill contains a hollow cylindrical shell that rotates about its axis. This The ball-milling process was carried out for the preparation of few-layered borophene using a planetary zirconia ball mill from Fritsch Pulverisette. The operational parameters of the ball-milling process Ball milling induced borophene flakes fabrication
احصل على السعر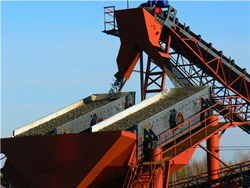
Manufacturing of Aluminum Flake Powder From Foil Scrap by Dry Ball
In the study of Hong et al. (2000), they produced flake powder from aluminum foil scrap by dry ball milling process using an inert argon and oxygen, and Nkwanyana and Loveday (2017) used batch grinding experiments in a 0.6 m diameter mill to test partial replacement of steel balls (37.5 mm) for secondary grinding, by partly rounded pebbles (19Addition of pebbles to a ball-mill to improve grinding
احصل على السعر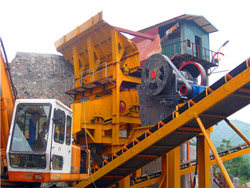
Process for dry milling zinc powder to produce zinc flake
The teaching focuses on the production of aluminum flake but also describes production of zinc flake in a ball mill using a mixture of mineral spirits and stearic acid as a lubricant. The apparatus used was a pebble mill loaded to 55% of it volume with 0.625 mm diameter stainless steel balls The mill was fitted with a cooling jacket throughFor the milling process, 40.12 g of the as-received Nb powder were loaded into two separate hardened steel containers of 125 ml volume with steel balls of 0.4 mm diameter, in a ball-to-powderWet ball milling of niobium by using ethanol, determination
احصل على السعر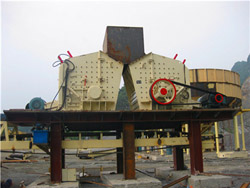
Flake Powder Metallurgy Encyclopedia MDPI
Flake powder metallurgy (FPM) including different processing routes, conventional FPM (C-FPM), slurry blending (SB), shift-speed ball milling (STY), and high-shear pre-dispersion and STY (HSPD/STY). The name of FPM was derived from the use of flake metal powders obtained by low-speed ball milling (LTY) from spherical powder. High-energy ball milling (HEBM) of powders is a complex process involving mixing, morphology changes, generation and evolution of defects of the crystalline lattice, and formation of new phases. This review is dedicated to the memory of our colleague, Prof. Michail A. Korchagin (1946–2021), and aims to highlight his works on the synthesis of Materials Development Using High-Energy Ball Milling: A
احصل على السعر
Method of producing metal flake Aluminum Company of
The mill was operated with open-circuit gas flow substantially as shown in FIG. 2. Alcoa grade 124 atomized powder containing 2.5 wt.% stearic acid of 97% purity was added at a rate of 13 lbs/hr. The mill employed a 520 lb. charge of steel balls having 1/4 inch diameter. The ball-to-metal ratio in the mill was about 10:1.US4065060A US05/730,181 US73018176A US4065060A US 4065060 A US4065060 A US 4065060A US 73018176 A US73018176 A US 73018176A US 4065060 A US4065060 A US 4065060A Authority US United States Prior art keywords mill metal flake balls solvent Prior art date Legal status (The legal status is an assumption and is not a legal US4065060A Metal flake production Google Patents
احصل على السعر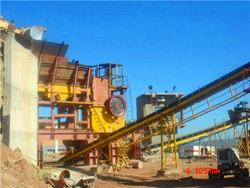
(PDF) Progress of Flake Powder Metallurgy Research
Behzad Sadeghi. P. Cavaliere. Flake powder metallurgy (FPM) including different processing routes, conventional FPM (C-FPM), slurry blending (SB), shift-speed ball milling (STY), and high-shearThe mill was operated with open-circuit gas flow substantially as shown in FIG. 2. Alcoa grade 124 atomized powder containing 2.5 wt.% stearic acid of 97% purity was added at a rate of 13 lbs/hr. The mill employed a 520 lb. charge of steel balls having 1/4 inch diameter. The ball-to-metal ratio in the mill was about 10:1.US4115107A Method of producing metal flake Google
احصل على السعر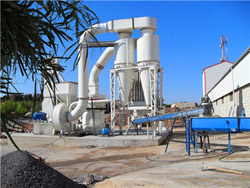
Aluminium Flake Pigments ResearchGate
Material and Ball Charges: The load of a grinding medium (steel ball) can be expressed in terms of the percentage of the volume of the mill that it occupies; i.e., a bulk volume of balls half1. Introduction. The flake-shaped metal powder has better electromagnetic [1], mechanical [2], and optical [3] properties than spherical or irregularly shaped powder.For example, although a strong demagnetization field generated inside the spherical or irregularly shaped particle degrades the magnetic properties, the demagnetization field Deformation type during the ball milling process: A
احصل على السعر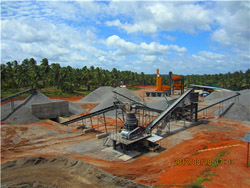
(PDF) Anisotropic SmCo5 flakes and
Abstract. This work is focused on the evolution of structure, texture and magnetic properties in SmCo5 powders during high energy ball milling (HEBM) in heptane with and without oleic acid (OAQuestion. 2 answers. Sep 15, 2023. if a 5gm of copper selenide in grinded to nanoparticles by a planetary ball mill by 550rpm, 250 ml cylinder, 50 balls (10mm diameter), with ball to powder ratio245 questions with answers in BALL MILLING
احصل على السعر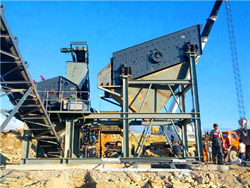
Ball milling: a green technology for the preparation and
Ball milling is a simple, fast, cost-effective green technology with enormous potential. One of the most interesting applications of this technology in the field of cellulose is the preparation and the chemical modification of cellulose nanocrystals and nanofibers. Although a number of studies have been repo Recent Review Articles Nanoscale Advances Most Popular Catalytic processes are critical steps in numerous industrial processes. The discovery of high reactivity of defects in metal-free two-dimensional materials has bolstered their emergence as catalysts. Here we consider the effect of defect-inducing methods in hexagonal boron nitride (h-BN) on their performance for olefin and CO2 Defect engineering in Boron Nitride for catalysis SpringerLink
احصل على السعر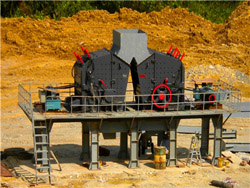
Ball Milling an overview ScienceDirect Topics
MLG flakes, 50 × 200 nm 2 [30] Planetary mill; steel balls (10 Ball mills, like the three roll machine, are a common occurrence in industry, for the production of fine particles. During the ball milling process, there are two factors that contribute to the exfoliation. The main factor contributing is the shear force applied by the balls.In this study, graphene was prepared using a QM-3B high-speed vibrating ball mill (specification: 80 ml; vibration frequency: 1200 r/min; motor specification: 220 V, 180 W) . 304 stainless-steel balls were used as grinding balls. The working principle is as follows: the high-speed rotation of the motor drives the cylinder to rotate at a highStudy on Preparation and Characterization of Graphene Based on Ball
احصل على السعر
(PDF) Ductile Metal Flakes based on (Au), (Ag), (Al
Based on milling experiments resolved by the High Energy (ball) Mill, the Simoloyer CM01-½l, with a grinding unit capacity of 0.5 l for laboratory purpose, a new grinding device, the Simoloyer(a) A schematic representation of physical cracking of graphite flake in a ball-mill crusher (500 mL) containing stainless steel balls (500.0 g, diameter 5 mm) agitated at 500 rpm for 48 h in the(a) A schematic representation of physical cracking of graphite flake
احصل على السعر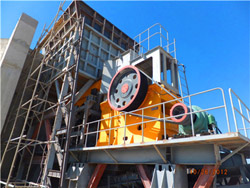
Manufacturing of Aluminum Flake Powder From Foil Scrap by Dry Ball
The weight of a stainless steel ball of diameter 16 mm is about eight times greater than that of a 9.6 mm ball (30.7 g vs. 3.8 g) although the number of 9.6 mm balls in the jar is larger than that
احصل على السعر