
clinker wet ball mill annum
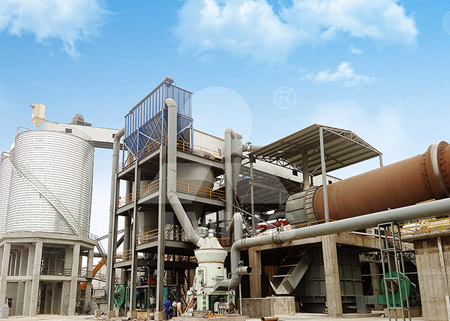
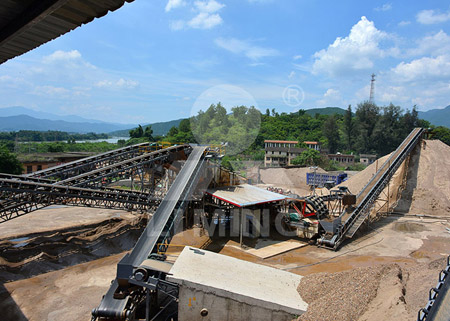
clinker wet ball mill annum
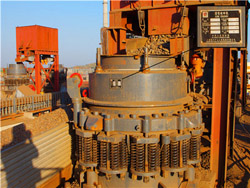
(PDF) Determination of granulometrical composition of the clinker
This paper presents results regarding the grinding behaviour of two batches of material (clinker) in a ball mill with its own two-step grinding process: the first ball mills. These type of . ball mills. in the coming decades will remain the basic units for grinding cement clinker and additives [3]. 2. Teoretical. The main task of IOP Conference Series: Materials Science and
احصل على السعر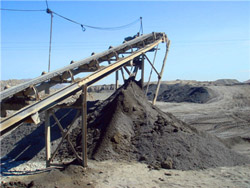
Modeling of closed-circuit ball milling of cement clinker via a
The aim of this theoretical study is to better understand the complex interplay between ball milling and air classification in full-scale two-compartment ball mills In the article attention is paid to improving the efficiency of production of fine powders, in particular Portland cement clinker. The questions of Portland cement clinker Matrix model of the grinding process of cement clinker in the ball mill
احصل على السعر
The effects of grinding media shapes on the grinding kinetics
Abstract. To investigate the effects of grinding media shapes on the grinding kinetics of ball mill cement clinker, the grinding effects with ϕ20 mm balls and ϕ20 × 20 Original Paper Published: 18 August 2022 Experimental study of clinker grinding in a ball mill and the behavior of the grinding media inside the equipment using Experimental study of clinker grinding in a ball mill and the
احصل على السعر
Experimental study of clinker grinding in a ball mill and the
Experimental study of clinker grinding in a ball mill and the behavior of the grinding media inside the equipment using DEM DOI: 10.1007/s43153-022-00261-3 Abstract. The use of high-pressure grinding rolls (HPGR) prior to ball mills has become a common practice in cement clinker grinding due to significant energy savings in comparison to ball milling alone.Ball-Mill Grinding Kinetics of Cement Clinker
احصل على السعر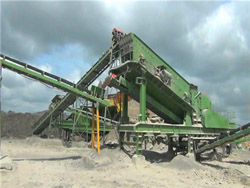
The effects of grinding media shapes on the grinding
To investigate the effects of grinding media shapes on the grinding kinetics of ball mill cement clinker, the grinding effects with ϕ20 mm balls and ϕ20 × 20 mm The results show that approximately 2.48t, 4.69t, and 3.41t of materials are required to produce a ton of the product in raw material preparation, clinker production, and cement grinding stages(PDF) Analysis of material flow and consumption
احصل على السعر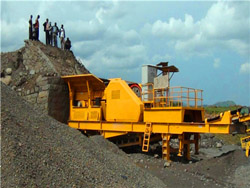
An overview of energy savings measures for cement industries
The current global consumption of cement industry is about 1.5 billion tons per annum and is rising at almost 1% per annum. Cement production requires approximately 110 kW h/t of electrical energy, with 40% directed to clinker grinding [26].Using real auditing, Avami and Sattari [17] investigated technological methods that would reduce the energy The size of grinding media is the primary factor that affects the overall milling efficiency of a ball mill (e.g. power consumption and particle size breakage). This article tackles the lack of aEffect of grinding media on the milling efficiency of a ball mill
احصل على السعر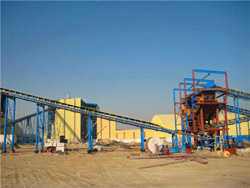
Evolution of grinding energy and particle size during dry ball
The balls mills were then compared based on several indicators of energy efficiency, productivity and processing speed. A study of different grinding aids for low-energy cement clinker production. 2023, Journal of the Southern African Institute of Mining and Metallurgy Grinding kinetics of quartz and chlorite in wet ball milling. PowderPortland cement clinker is a hydraulic material which shall consist of at least two-thirds by mass of calcium silicates (3CaO.SiO 2 and 2CaO.SiO 2), the remainder consisting of aluminium and iron containing clinker phases and other compounds.The ratio of CaO to SiO 2 shall not be less than 2.0. The magnesium oxide content (MgO) shall not exceed 5.0% Portland Cement Clinker an overview ScienceDirect Topics
احصل على السعر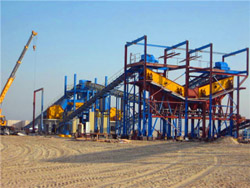
Rashmi Cement Expansion Plan-CEMENT PDF PDF Mill
Traditionally, plants used ball mills to grind clinker and gypsum into cement. The result: the majority (60%) of finish grinding in the world is still performed using the ubiquitous ball mill. Ball mills are cylindrical steel shells with steel liners. These rotating drums contain grinding media that tumble inside the cylinder.Grinding: The grinding of the crushed materials is carried out in two stages; first by ball mill and then by tube mill. Materials from ball mill to tube mill are conveyed by means of a screw driver. Before grinding, the material is mixed with 30- 40 % water by weight. Ball mill grinding: The ball mill consists of a cast Tube mill grinding: FromCement Lecture Note AAI PDF Cement Mill (Grinding)
احصل على السعر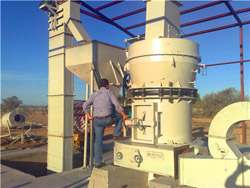
Energy and exergy analyses for a cement ball mill of a new
Nowadays, ball mills are used widely in cement plants to grind clinker and gypsum to produce cement. In this work, the energy and exergy analyses of a cement ball mill (CBM) were performed andMeanwhile, the grinding rate of the rod mill was higher than the ball mill [22]. The equivalent granule size declined while its specific surface area increased gradually with grinding time [23]. The grinding kinetics of quartz and chlorite followed the first-order breakage behavior in wet ball milling [24].An innovative approach for determining the grinding media
احصل على السعر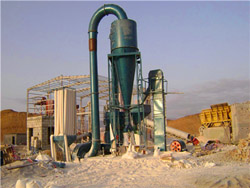
The generation of power from a cement kiln waste gases: a
The plant produces Portland Pozzolana Cement and the product is finely ground using closed circuits ball mills to guarantee product quality with respect to achieving the target compressive strengths within a set time. Power interruptions constitute a plant downtime of an average 2% of total production time per annum. 350 kJ/kg clinkerThis clinker is then ground in a ball-mill together with gypsum and other additives to produce cement. (GJ tonne −1 clinker) Wet process with internals: 5.86–6.28: Long dry process with internals: 4.60: 1-Stage cyclone preheater be expected to result in the production of over 62,500 tonnes of solid waste and over 350×10 6 L ofCement Kiln Process Modeling to Achieve Energy
احصل على السعر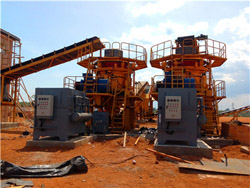
Project Report On Cement Plant Using Clinker (Crushing Plant)
PROJECT REPORT ON CEMENT PLANT USING CLINKER (CRUSHING PLANT) Free download as PDF File (.pdf), Text File (.txt) or read online for free. Cement is a material that binds together solid bodies (aggregate) by hardening from a plastic state. Many materials act as adhesives or cement according to this definition. The cement : Blaine fineness, residue, ball mill, grinding, cement. Introduction: The world cement production has been increasing constantly since the early 1950s, especially in developing countries [1]. Current world consumption of cement is about 1.5 billion tonnes per annum and it is increasing at about 1% per annum [2].Effect of Feed Amount and Composition on Blaine and
احصل على السعر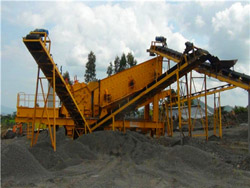
Cement Grinding Optimization PDF Mill (Grinding)
The efficiency of fine grinding in the second compartment is largely controlled by the size of grinding balls. Due to limitation of the mills rotational speed, the smallest ball size is usually restricted to about 15 mm. Cement grinding using stirred mills (Pilevneli and Azizli, 1999) indicates that using smaller media (5-8 mm range) improvesA novel approach for modelling of physical interactions between slurry, grinding media and mill structure in wet stirred media mills. Miner. Eng., 148 (2020), p. The effects of grinding media shapes on the grinding kinetics of cement clinker in ball mill. Powder Technol., 235 (2013), pp. 422-425. View PDF View article View in Scopus An innovative approach for determining the grinding
احصل على السعر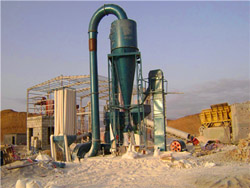
A comparative analysis of steel and alumina balls in fine
Fig. 2 shows the timewise evolution of the cumulative PSD experimentally obtained from the laboratory batch ball mill with different single ball sizes (i.e., d B = 20, 30, and 40 mm) using steel balls and alumina balls. As milling progressed and finer particles were generated by breakage, the PSD shifted to the left monotonically even in the fine The grinding circuit at PT Newmont Nusa Tenggara (PTNNT)-Batu Hijau mine consists of two SABC (semi-autogenous milling, ball milling, pebble crushing) trains, including four 20 x 33'6" ball millsAlex JANKOVIC Principal Consultant / Mineral Processing
احصل على السعر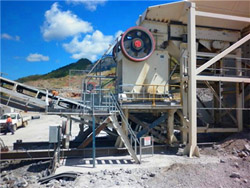
DESIGN AND ANALYSIS OF BALL MILL INLET CHUTE FOR
(Unidan Mill S) type FLS Ball mill which are used in the Cement industry for grinding clinker material. The present mill inlet chute can be used for the two compartment ball mills only in which primary and finish grinding both are takes place. It may be a closed or open circuit grinding systems.The effects of grinding media shapes on the grinding kinetics of cement clinker in ball mill. Powder Technol. (2013) K.J. Reid A solution to the batch grinding equation. Chem. Eng. Sci. The optimal media proportion was φ 50 mm: φ 40 mm: φ 30 mm = 28%: 28%: 44% via wet grinding experiment, in which the yield of qualified Effects of circulating load and grinding feed on the grinding
احصل على السعر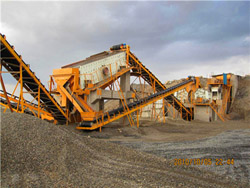
sbm/sbm suitable assumptions for gypsum and clinker in ball mill
sbm suitable assumptions for gypsum and clinker in ball millComposition Of Gypsum In Ball Mill Composition Of Gypsum In Ball Mill , We is a large sized joint stock enterprise integrated with the scientific research,production and sales of heavy mining machinery.It is located in high and new technology industrial development zone,Zhengzhou with an area
احصل على السعر