
grinding systems plants
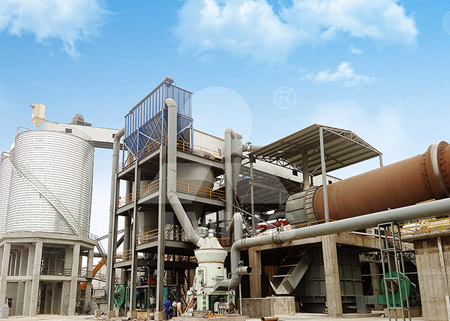
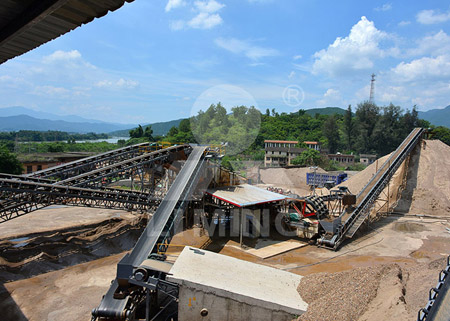
grinding systems plants
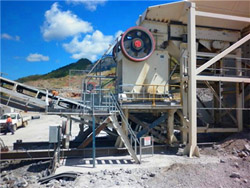
Grinding Plants Pulverizing Systems JEHMLICH
Customized Fine Grinding Plants. The REKORD series of GMP- and industrial mills are the core element of our tailored grinding plants. The JEHMLICH modular system provides a full set of individual solutions for The processing of legumes, acorns, nuts and USOs, as well as of ferns and aromatic plants, has been traced on grinding tools in order to examine their wider Use-wear analysis of grinding tools and the exploration of plant
احصل على السعر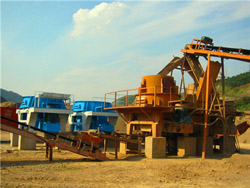
Energy-Efficient Technologies in Cement Grinding
In this chapter an introduction of widely applied energy-efficient grinding technologies in cement grinding and description of the All grinding processes in the cement industry are operated dry. The capacities of grinding mills range from 300 − 1000 TPH for Limestone and for cement Review on vertical roller mill in cement industry & its
احصل على السعر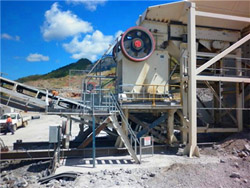
Model and simulator of inlet air flow in grinding installation
To better leverage the device’s potential, a grinding system was designed, patented and built 19,20,21. The installation includes underpressure transport of the By consuming the lowest specific energy per ton of any kind of target product, the combination of a roller press and modern separator technology, known as KHD Comflex® & GrindC® Grinding...(PDF) MULTIPLE MATERIALS, ONE SOLUTION
احصل على السعر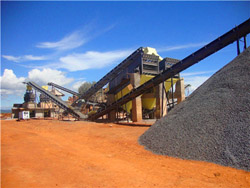
An industrial comparative study of cement clinker grinding systems
The same lots of Portland cement clinker and natural gypsum (CaSO 4.2H 2 O) were used in this industrial-plant-scale experimental work to eliminate the potential A review of the literature shows that there are numerous studies on energy consumption comparing conventional grinding systems and VRM in cement plants. It is worth noting that the VRM could save Minerals Free Full-Text Analysis and
احصل على السعر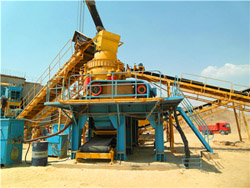
Laboratory Agitator Bead Mill LabStar Grinding
The multi functional laboratory mill LabStar enables scientific academic work on difficult research and development tasks and impresses with its easy handling.. The laboratory mill LabStar is the Section snippets Experimental work. The same lots of Portland cement clinker and natural gypsum (CaSO 4.2H 2 O) were used in this industrial-plant-scale experimental work to eliminate the potential effects of variations in the feed to the grinding systems. Chemical compositions of the clinker and the gypsum, measured by X-ray An industrial comparative study of cement clinker grinding systems
احصل على السعر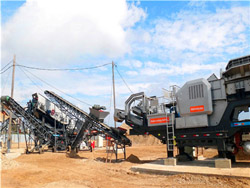
Operational parameters affecting the vertical roller mill
In literature, there are many studies performed in cement plants on comparison of conventional grinding systems and vertical roller mills in terms of energy consumption. It was noticed that 30% energy saving could be provided by VRM for cement grinding (Schaefer, 2002).The final manufacturing stage at a cement plant is the grinding of cement clinker from the kiln, mixed with 4-5% gypsum and possible additives, into the final product, cement . In a modern cement plant the total consumption of electrical energy is about 100 kWh/t . The cement grinding process accounts for approx. 40% if this energy consumption.CEMENT GRINDING SYSTEMS INFINITY FOR CEMENT EQUIPMENT
احصل على السعر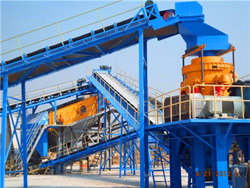
Impact of the Drying Temperature and Grinding Technique
The research was carried out on a mill with a knife and hammer grinding system, which is the most popular in the fragmentation of biomass. The analysis of particle size distribution and bulk density of the obtained material was carried out.,perennials like Cup plant, Virginia mallow, or willowleaf sunflower of 22, 26, and 38%Paint NETZSCH Grinding & Dispersing. Paint is a coating material based on organic binders and, depending on the composition of the binding agent, can contain organic solvents and/or water. The organic or inorganic pigments that are finely dispersed in the binder give the paint its color. In general, paint is composed of binders, Paint NETZSCH Grinding & Dispersing
احصل على السعر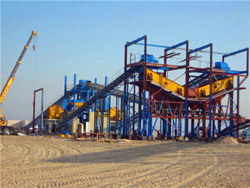
Energy-Efficient Technologies in Cement Grinding IntechOpen
The energy consumption of the total grinding plant can be reduced by 20–30 % for cement clinker and 30–40 % for other raw materials. The overall grinding circuit efficiency and stability are improved. The maintenance cost of the ball mill is reduced as the lifetime of grinding media and partition grates is extended. 2.5.Process technology for separate grinding on the other hand is well known in general. In most cases existing mill systems can be enhanced by transport and storage facilities. But depending on the given plant layout and the product portfolio the individual technical solutions for separate grinding and blending can significantly differ.Process technology for efficient and sustainable cement
احصل على السعر
Modeling of energy consumption factors for an industrial
Cement production is one of the most energy-intensive manufacturing industries, and the milling circuit of cement plants consumes around 4% of a year's global electrical energy production. It isThe bottom line: The polycom® HPGR has under suitable conditions a technically as well as economically superior concept compared to conventional systems. As a central component of a modern finish grinding plant, the high-pressure grinding roll mill consumes only 40 to 50 percent of the energy compared to the classic ball mill and is thus the most polycom® HPGR cutting-edge technology in the cement
احصل على السعر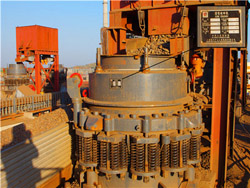
Actuators Free Full-Text Electromechanical
The robotic grinding system for a thin-walled workpiece is a multi-dimensional coupling system composed of a robot, a grinding spindle and the thin-walled workpiece. In the grinding process, a dynamic Raw meal grinding is a vital link in the cement raw material preparation process. After the cement raw material is crushed, it will be sent into the raw mill for further grinding until a certain degree of fineness is reached, and then enter the clinker calcination process. From the production experience of many cement plants, the selection ofRaw Mill Raw Mill In Cement Plant AGICO Cement Raw Mill
احصل على السعر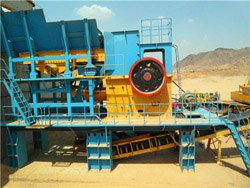
Design of Robot System for Grinding the End of
According to the functional analysis, the robot system for grinding the end of reactor core in heavy water reactor nuclear power plant is mainly divided into the grinding part, the video part and the plane The grinding of cereals has been shown to have predominated, but legumes, nuts and grass plants also played a major role. Nonetheless, depending on the region and cultural background, different types of grinding systems were employed, suggesting a strong link with varied food habits throughout the continent.Use-wear analysis of grinding tools and the exploration of plant
احصل على السعر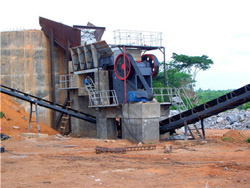
NETZSCH Alpha® NETZSCH Grinding & Dispersing
The new NETZSCH Alpha® modular machine platform is designed such that four different grinding systems can be mounted on the same platform according to a defined drive capacity: the advanced disk grinding system, Discus, the Zeta® system with optimized grinding media separation, the new peg system, Macro and the new grinding The Easy Grinding System is an innovative modular design from CETEC, which facilitates the cement producers to quickly occupy the new and growing market. Plant Upgrade After the upgrading and modification by CETEC the plant will be operated with a higher efficiency in the view of both economic output and environment protection.信泰
احصل على السعر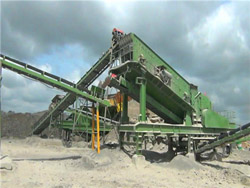
Wet Grinding NETZSCH Grinding & Dispersing
NETZSCH is one of the market leader in wet grinding technology. The bundling of process-related know-how and the extensive machine program from laboratory to production machines to complete production lines is our strength. Agitator bead mills are grinding machines for ultra-fine processing of solids in liquids. Their area of application There are three types of grinding media that can be used in ball mills of cement plants. 1. Steel Balls. Steel balls are one of the most widely used grinding media in cement ball mills, their diameters can range from 20mm to 120mm according to different grinding requirements. In a cement ball mill, generally, φ50–100mm steel balls are usedHow to choose proper grinding media for your ball mill
احصل على السعر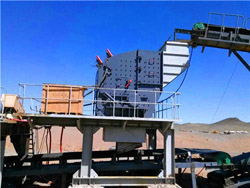
Horizontal Disk Mill Discus NETZSCH Grinding & Dispersing
The horizontal disk mills Discus are improved, continuous working laboratory and production machines for wide variety of applications. The disk agitator shaft activates the grinding media with high intensity through the entire grinding chamber. Highly efficient separation devices that are adapted to your application are available for
احصل على السعر